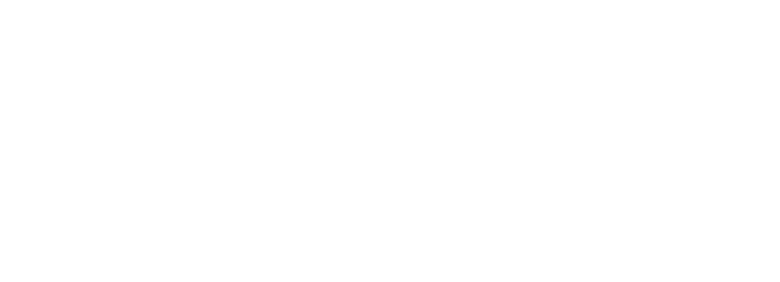
世界中のお客さまにタイムリーに製品を届ける。月5000件の“カイゼン”で一番の品質を目指す!
- ホーム
- コラム(インタビュー)
- ものづくり最前線(8)
生産部第一課
志水 悟
生産部生産技術課
土屋 悟
生産部第一課
柳沢 憲志
私は,入社して無停電電源装置(UPS)の設計業務に従事していました。その後営業・設計を経て,生産部に来たのはここ3年くらいです。現在は,小容量・中容量の無停電電源装置,太陽光発電用パワーコンディショナなど組立工程全般の管理をおこなっています。
私は,生産技術をやっています。主な仕事内容ですが,一番は設備の製作。社内で導入している「生産誘導システム」を作ったり,生産にかかわる新規設備の導入・整備・改善,冶具や工具の設計・手配,工場のレイアウト,工事などを全般的におこなっています。
入社時にパワーシステム事業部生産第一課に配属されてから,小容量UPSの組み立て一筋で今に至ります。
富士山工場パワーシステム事業部では,主にUPS,10~100kWの太陽光発電用パワーコンディショナ,エンジンジェネレータを製造しています。最近では,その他にも瞬低補償装置,ピークカット装置など新製品も出てきています。
特長としては,小容量UPSの組立ラインに,自社開発の「生産誘導システム」を導入して組み立てをおこなっていることですね。これは,簡単にいうと写真つきの作業手順書を電子化したようなものです。紙の作業手順書だと,作業者が読み飛ばすとそのまま工程が飛んでしまいますが,このシステムでは,そのときおこなう作業指示がパソコンの画面に表示され,その作業が完了しないと,次の作業指示に進まないようになっています。作業誘導により,工程飛ばしなどのポカミスを防止しているのです。また,使用する工具も指示され,ねじ締めの場合,正しい電動ドライバーでねじを締めたときトルクアップ信号で次の指示に進みますが,間違えて違うドライバーで締めると次の指示に進みません。使用する工具も間違えようがないのです。
これまで,作業者のポカミスが多かったのですが,このシステムを導入することによって作業者のミスがなくなり,製品の不具合が0に近い状態になりました。
UPSは部品点数が多く,作業工程数を計算すると何千工程にも及ぶのですが,作業者の経験と感覚でやっていた部分も多かったので,「生産誘導システム」を導入する際は,人とシステムをどう融合させるかというのが一番ポイントでした。
やはり品質というのが一番です。ただ,品質のためならゆっくりやってもいいのか?というと,そうはいかないので,組立工数を下げながら,かつ品質のいいものを作り上げるというのを目指しています。工数低減・作業改善の取り組みとして,2008年度から「高収益モノつくりプロジェクト」を実施しています。
2008年度の標準工数を基準に生産性を200%にするという目標を立てました。今の人数で倍のものを作る,もしくは半分の人数で現状を維持しましょう,ということですね。この目標は,4年かけて2012年度に達成しました。そこで,目標をリセットして2013年度から2012年の標準工数を基準に生産性120%を目標に継続して取り組んでいます。6グループに分かれて月1回「改善会」を開催し,作業の無駄や,人が歩く無駄,そういった無駄を排除する取り組みを継続的に実施しています。改善会で出た内容はすぐに工程に反映させて,3ヶ月に1度,報告会を開いています。
そうですね。今となっては,初めの目標が例えば130%というより,逆に高い目標にして200%を狙ったのが良かったかなと思います。大胆な考えが出てきたと思います。
先にスタートした「5S活動(*)」と融合して,まずは,スペースを半分,組立ラインの長さを半分,組み立てる時間を半分にしましょうという取り組みを実施しました。また,設計部門・品質管理部門と協力し,構造や製品の見直しなどを平行しておこないました。
私たちが現場で最初におこなったのは,作業分析です。例えば,作業者に付きっきりで歩数を数えて,作業中に3歩歩いていたら,歩かなくて良いレイアウトにしましょうといった具合に,とにかく作業スペースを詰めました。でも,詰めすぎると逆に作業性が悪くなる問題が発生するなど,その分析が一番大変でしたね。
「5S活動」も「高収益プロジェクト」も,最初はなかなか改善の案も出てこなくて…みなさん少しやらされ感があったんですね。ですが,生産性が上がってきたというのが実感できると改善することが楽しくなって,改善が習慣になっていきました。
今では,生産部のメンバー約100人で,月平均4000件~5000件の改善が出てきます。
また最近では,太陽光発電用パワーコンディショナの組立ラインにタブレットを導入しました。今までは,10cmの重い作業手順書のファイルを所定の場所に置いて,それを見に行きながら作業していたので,結構大変だったんです。タブレットにしてからは組み立てをおこなう場所の近くまで持っていって作業できるようになり,作業内容の確認が容易にでき,作業効率がアップしました。作業手順書は,実際の作業に合うよう常に見直しをおこなっているので,タブレットシステムにしてから管理も簡単になりました。
*5S活動:職場環境の維持・改善で用いられるスローガンとして,各職場で徹底するべき事項を5つにまとめたもの。整理・整頓・清掃・清潔・躾の5つ。整理・整頓・清掃から始めて人の意識を変える取り組み。
品質のいいものを市場に投入するというのが一番ですね。毎朝朝礼を開いて,各職場のメンバーにも常に品質について考えながら仕事をしてもらうよう意識付けをしています。さらなる高品質な製品を,お客さまが欲しいときにタイムリーに供給できるような体制を構築していきたいです。
同じく品質がやっぱり一番。お客さまに「使ってよかった」と言っていただけるような,いい製品を届けるという使命を持ってます。私は,工場の組立ラインや設備など,作業環境を見ていますので,設備を作るうえでも,作業環境を改善するうえでも,常にいい品質を保つためには,どういった環境づくりがいいかというのを常に考えています。
また,お客さまに一日でも早く製品を届けられるように,日々リードタイムを縮めるよう努力しています。
私も品質を最優先に仕事に取り組んでいます。毎朝の朝礼で,品質について日替わりで発表をおこないます。自分で話すことで品質に対する意識が非常に高くなりますし,発表を聞いたメンバーも情報を共有化することで,気をつけなければいけないこと,気づかされる点もあります。
世界中のお客さまに安心して使ってもらえる製品を作って,山洋電気の製品を買って良かったと喜んでいただける,そういったものづくりをしていきたいです。
公開日: 2018-01-08 00:00