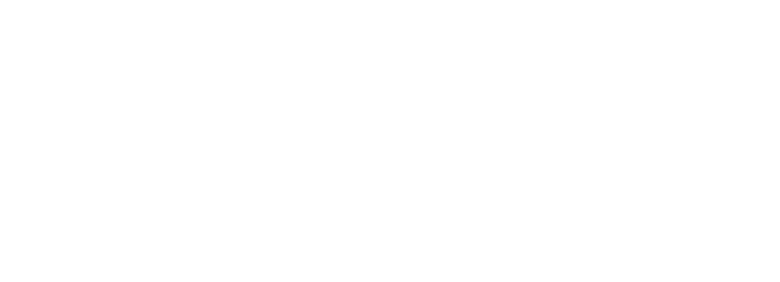
Unternehmen B, ein Hersteller von Industriemaschinen, wollte seinen Anteil am Neuwagenmarkt erhöhen, der aufgrund des Aufkommens von Öko-Autos wie Hybridautos und Elektrofahrzeugen expandierte. Insbesondere im Großraum China hat sich in den letzten Jahren die Automatisierung beschleunigt, um die Arbeitskosten zu senken. Da es sich um einen Markt handelt, der voraussichtlich schnell wachsen wird, ist es sicher, dass der Erfolg oder Misserfolg beim Erwerb von Marktanteilen große Auswirkungen auf das zukünftige Geschäft von Unternehmen B haben wird. Unter diesen Umständen benötigte auch Unternehmen B eine schnelle Bestückungsmaschine für den neuen Leiterplattenherstellungsprozess.
Unternehmen B musste schnell Ergebnisse liefern, um auf sich ändernde Marktanforderungen reagieren zu können. Um die Entwicklungsvorlaufzeit zu verkürzen, erwog das Unternehmen eine Erneuerung der Maschine durch Wiederverwendung der Anwendungen der aktuellen Maschine. Als ich es jedoch überprüfte, stellte ich fest, dass das Programm in einer Landessprache geschrieben worden war, die damals in Japan gängig war, da die Spezifikationen zehn Jahre alt waren, und dass sein Inhalt nur für die damaligen Entwickler verständlich war. Es ist.
Zu dieser Situation sagt Manager S der Systemdesignabteilung von Unternehmen B Folgendes: „In den letzten zehn Jahren hat sich die Software rasant verändert, und die Industriemaschinen, die wir bisher entwickelt haben, waren stark von den Personen abhängig, die in diesen Jahren an der Entwicklung beteiligt waren. Darüber hinaus haben viele der Entwickler das Rentenalter erreicht. Ich bin gegangen.“ das Unternehmen. Die fehlende gemeinsame Nutzung des Unternehmensvermögens war ein schwerer Schlag.
Darüber hinaus trat ein Problem bezüglich der Systemkonfiguration auf. Da die Antriebssystemausrüstung (Steuerungen, Servomotoren, Schrittmotoren usw.) herstellerübergreifend optimiert wurde, erschwerte der Anschluss der Steuerung an Geräte mehrerer Hersteller nicht nur die Verkabelung, sondern erhöhte auch die Anzahl der für die Verkabelung der Maschine erforderlichen Arbeitsstunden Dies führte dazu, dass die Anzahl der nach der Lieferung erforderlichen Wartungsschritte zunahm.
„Diese Probleme sind ein Faktor, der uns daran hindert, die Entwicklungsvorlaufzeiten zu verkürzen. Zunächst mussten wir unsere Entwicklungsumgebung von Grund auf überprüfen, einschließlich unorganisierter interner Ressourcen.“
Herr S. wandte sich wegen dieser Probleme an SANYO DENKI, da das Unternehmen bereits Erfahrung mit der Implementierung einiger seiner Servosystemprodukte hatte. Nach einem Gespräch mit einem Vertriebsmitarbeiter erfuhren wir, dass sich viele dieser Probleme durch den Einsatz der Controller des Unternehmens beheben ließen. Außer der Lieferung von Geräten übernimmt SANYO DENKI auch die Auftragsentwicklung und stellt die Technologie für den Aufbau optimaler Systeme bereit. Auch dieses Supportsystem war für Herrn S. interessant. Unternehmen B entschied sich umgehend für die Einführung des Bewegungsregler SANMOTION C von SANYO DENKI.
Zunächst analysierten Unternehmen B und SANYO DENKI das Anwendungsprogramm der vorhandenen Ausrüstung und begannen damit, es in der PLC-Programmiersprache (IEC61131-3) neu zu schreiben, die von PLCopen weltweit standardisiert wurde und von SANMOTION C verwendet wird. Durch die Verwendung einer standardisierten Sprache ist es Ingenieuren möglich geworden, Programminhalte gemeinsam zu nutzen und Software in einen Vermögenswert umzuwandeln. Wenn Unternehmen B ein abgeleitetes Modell entwickelt, erleichtert diese strukturierte Programmierung außerdem die gleichzeitige Entwicklung verschiedener Geräte. Dies führte zu einer dramatischen Steigerung der Effizienz der Softwareentwicklung.
Die Wünsche der Firma B zur Erneuerung ihrer Bestückungsmaschine bestanden darin, die Anzahl der Bauteiltypen von maximal 36 bei der Vorgängermaschine auf maximal 48 zu erhöhen, sowie die Bestückungsgeschwindigkeit und Bestückungsgenauigkeit zu verbessern. Als Antwort hierauf schlug SANYO DENKI ein System vor, das gleichzeitig 11 Servomotorachsen und 8 Schrittsysteme mit geschlossenem Regelkreis steuern konnte. Darüber hinaus konnten wir durch die individuelle Anpassung die optimale Kombination erreichen und die Anforderungen von Unternehmen B erfüllen.
Darüber hinaus ist „SANMOTION C“ mit einer Vielzahl von Feldbussen erhältlich, einschließlich EtherCAT, was den Verdrahtungsaufwand innerhalb des Geräts reduziert, die Montagezeit verkürzt und die Wartungsfähigkeit verbessert.
Durch verschiedene Verbesserungsmaßnahmen konnte Unternehmen B die Entwicklungsvorlaufzeit um fast 50 % reduzieren. Wir haben außerdem eine Reduzierung der Wartungsarbeitsstunden um 40 % erreicht.
Herr S fasste die Erneuerung wie folgt zusammen: „Der Vorschlag von SANYO DENKI beschränkte sich nicht nur auf den Controller, sondern war optimal für das gesamte System. Die Entwickler reagierten direkt auf technische Anfragen, wodurch wir Probleme schnell lösen konnten, und sie boten uns stets flexible Unterstützung, die unseren Bedürfnissen entsprach.“
Komplettlösungen wie diese von SANYO DENKI werden die neuen Geschäftsvorhaben von Unternehmen B auch weiterhin unterstützen.
Veröffentlichungsdatum: