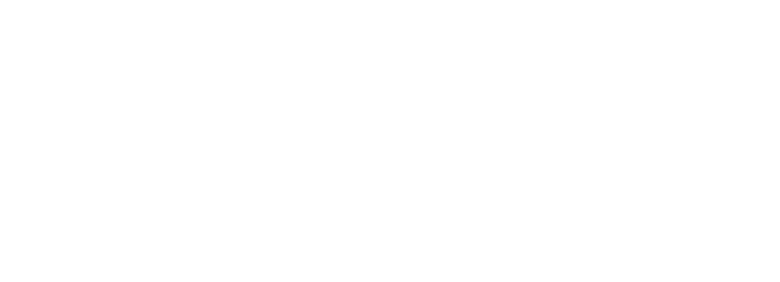
Automobil- und Elektronikhersteller bemühen sich stärker als je zuvor um eine Verbesserung der Qualität. Teilehersteller und andere kooperierende Unternehmen führen ebenfalls aktiv Präzisionsmessgeräte in ihre Produktionslinien ein, um die Produktqualität zu verbessern, ohne dass menschliches Eingreifen erforderlich ist.
Vor diesem Hintergrund befand sich der Messgerätemarkt in den letzten Jahren in einem Expansionstrend. Allerdings wird der Wettbewerb unter den Messgeräteherstellern immer intensiver, da die Anforderungen an „hohe Präzision“, „hohe Zuverlässigkeit“, „Kompaktheit“ und natürlich „niedriger Preis“ immer strenger werden.
Unternehmen E, das verschiedene Messgeräte entwickelt und herstellt, hat ein Projekt zur Entwicklung einer kleinen Präzisionsmessmaschine gestartet, die in Produktionslinien integriert werden kann, um seine Wettbewerbsfähigkeit zu stärken.
Herr M, der Entwicklungsleiter von Firma E, sagt:
„Präzisionsmessgeräte werden nicht nur in Abteilungen wie Forschung und Entwicklung sowie Qualitätskontrolle eingeführt, sondern auch an Produktionsstandorten. Daher ist ein qualitativ hochwertiges Gerät erforderlich, das auch an Produktionsstandorten stabil und mit hoher Genauigkeit messen kann.“ Dort, wo sich die Temperatur schnell ändert, handelt es sich außerdem um ein kompaktes und kostengünstiges Gerät, das direkt am Produktionsstandort installiert werden kann.
Mit der Ausweitung der Anwendungen und Nutzungsmöglichkeiten entstehen auch neue technologische Herausforderungen.
„Wenn Sie ein Stromversorgungssystem mit der in Fabriken verwendeten 200-V-Wechselstromversorgung aufbauen, wird die Steuerausrüstung zwangsläufig größer. Außerdem werden die Teile groß und teuer. Darüber hinaus sind die Sicherheitsstandards für Hochspannung streng, was ein Hindernis darstellt.“ Miniaturisierung.
Aus diesem Grund haben wir uns entschieden, das Stromversorgungssystem mit DC48V oder weniger zu konfigurieren. Wir dachten, dass wir dadurch die Größe und die Kosten der Steuerungsausrüstung deutlich reduzieren könnten. Um die Anlagen zu verkleinern, haben wir uns außerdem dazu entschlossen, einen Servoverstärker im eigenen Haus herzustellen, dessen Form dem verfügbaren Platz in der Anlage entspricht. ” (Herr M)
Nachdem sich Unternehmen E für eine Politik der Verkleinerung und Kostenreduzierung entschieden hatte, beschloss es, nach dem am besten geeigneten Servomotor zu suchen.
Ich suchte nach einem Motor, der mit 48 V Gleichstrom oder weniger betrieben werden kann, und wiederholte Tests, aber ...
„Da wir die Spannung gesenkt haben, mussten wir den durch den Motor fließenden Strom erhöhen, um die gleiche Anzahl an Umdrehungen zu erzeugen. Außerdem wurde die Motorgröße von 73 mm im Quadrat geändert, um das Gerät kompakter zu machen Das Vorgängermodell erzeugte daher viel Wärme, was dazu führte, dass sich das Metall thermisch ausdehnte, was zu Temperaturschwankungen führte. Um eine hohe Messgenauigkeit zu erreichen, mussten wir die Hitze unterdrücken „Wir haben die Wärmeerzeugung so weit wie möglich erhöht, aber ganz gleich, welchen Motorhersteller wir ausprobiert haben, die Wärmeerzeugung hat den zulässigen Wert überschritten.“ (Herr)
Die Entwicklung gerät ins Stocken und Herr M. steht vor der schwierigen Aufgabe, sowohl „Miniaturisierung“ als auch „hohe Präzision“ zu erreichen.
Auf der Suche nach einer Lösung kontaktierte Herr M einen Vertriebsmitarbeiter von SANYO DENKI, einem Hersteller von DC-Servosysteme, und besprach diese Probleme mit ihm. Sie schlugen also vor, „den Gleichstrom-Servomotor anzupassen und zu optimieren“, und wir baten sie sofort, diese Aufgabe zu übernehmen.
SANYO DENKI lieferte bald einen Prototyp mit Wicklungsspezifikationen, die speziell auf die Anforderungen der E Company zugeschnitten waren. Nach Erhalt des Motors begann Unternehmen E sofort mit dem Einbau in eine echte Maschine und der Durchführung von Tests.
Dieses Gerät verwendet einen dreiachsigen Gleichstrommotor. Sie haben einen Motor entwickelt, der genau die Geschwindigkeit und das Drehmoment erzeugen kann, die für alle drei Achsen erforderlich sind. Ich war erstaunt über ihr hohes Maß an Fachwissen und technischem Geschick bei der Feinabstimmung der Wicklungen.
Allerdings überschritt die Temperatur auf der Y-Achse den zulässigen Grenzwert leicht. Da die Konfiguration einen schlechten Lastwirkungsgrad aufwies, musste der Strom erhöht werden, um die Zieldrehzahl zu erreichen, was zwangsläufig zu einer starken Wärmeentwicklung führte. Da die Motorleistung aufgrund von Montagebeschränkungen nicht erhöht werden konnte, entschieden wir uns, die Struktur rund um die Last zu verbessern.
Anschließend befasste sich ein Motordesigner von SANYO DENKI gemeinsam mit uns mit der Problematik der Wärmeentwicklung, gab Ratschläge und beurteilte dabei auch die Wärmeableitungswege und den Luftstrom. Ich war mit ihrer freundlichen Einstellung bei der gemeinsamen Problemlösung zufrieden. „ (Herr M)
Durch die Feinabstimmung der Wicklungsspezifikationen und die Erhöhung der Effizienz der Motorwärmeableitung auf der Maschinenseite ist es uns gelungen, die Motoroberflächentemperatur um mehr als 10 °C zu senken. Als es Herrn M. gelang, die Wärmeentwicklung in akzeptablen Grenzen zu halten, kam er zu der Überzeugung, dass es möglich sei, das Gerät sowohl kleiner als auch präziser zu machen.
Darüber hinaus schlug SANYO DENKI vor, die Motorwelle anzupassen, sodass die Riemenscheibe des Vorgängermodells wiederverwendet werden konnte. Diese umfassende Unterstützung war für Unternehmen E der entscheidende Faktor bei der Einführung der DC-Servomotoren von SANYO DENKI.
„Dieses Mal dachten wir darüber nach, einen Gleichstrom-Servomotor mit kleiner Kapazität und hoher Reaktionsfähigkeit bei niedrigen Geschwindigkeiten zu verwenden und einen Verstärker im eigenen Haus herzustellen, um eine höhere Präzision, kleinere Größe und geringere Kosten für die Ausrüstung zu erreichen, aber es erzeugte Wärme.“ Durch die Lösung dieser Probleme konnten wir erfolgreich einen Gleichstrom-Servomotor einsetzen und die Installationsfläche der Messmaschine erfolgreich um 40 % reduzieren. Außerdem stellten wir fest, dass wir durch die Produktion eines Verstärkers im eigenen Haus unnötige Funktionen eliminieren konnten „Kosten um 30 % senken.“ (Herr M)
Einige Monate später, nach erfolgreichem Abschluss der Entwicklung des Messgerätes, äußerte sich Herr M. wie folgt:
„Ich bin erleichtert, dass wir unser Entwicklungsziel erreichen konnten, das fast in eine Sackgasse geraten wäre. Ich bin sehr dankbar für die detaillierte Anpassung sowie die Berücksichtigung der Kosten. Ich werde mich in Zukunft auf jeden Fall zuerst an SANYO DENKI wenden, wenn ich auf schwierige Probleme stoße.“
Veröffentlichungsdatum: