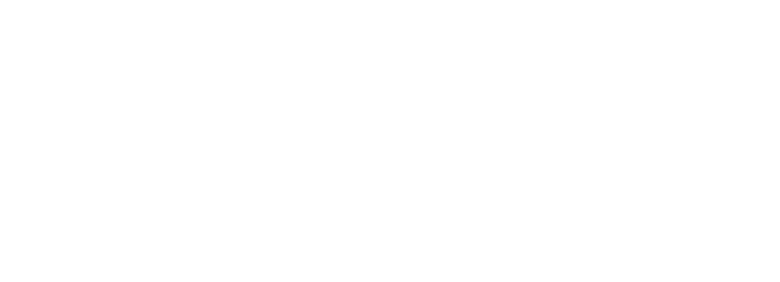
設計部
石原 勝充
設計部
村松 陽
設計部
戸田 貴久
設計部
漆本 光瑠
私は2001年に入社して,もう16年経ちました。ファンの設計開発では,主にフレーム,羽根など構造設計を担当しています。今回のエアフローテスターでも,構造設計をメインに担当しました。
私は2002年に入社し,ずっとファンの回路の設計を担当しています。そのうち3年間は台湾にいました。今回開発したエアフローテスターでは操作部の設計を担当しました。
1997年入社なので,今年でもう20年になります。最初はステッピングモータのドライバをやっていましたが,その後はファンの回路とソフトの開発を担当しています。今回の開発では基板のプログラム全般を担当しています。
私は入社して今年で3年目です。普段はファンの回路をやっています。エアフローテスターの開発では主に評価試験を担当しています。
まずは,この製品は何のために使うのか,というところから説明します。
装置の中に部品がたくさんあると,風が流れにくくなります。それを通風抵抗が大きい装置といいます。通風抵抗とは風の流れにくさを表します。その通風抵抗を数値化するために,ダブルチャンバー測定装置という測定器がありますが,本体が非常に大きくて高額なので,基本的にファンメーカーや一部の装置メーカーしか持てないのが現状です。
それを可搬式にして,多くの人が手軽に測定できることを実現したのが,このエアフローテスターです。
実は,開発のきっかけは社内の営業ツールとして使いたいという要望でした。
最近,低消費電力ファンや高静圧ファンなどを発売しているのですが,その特長を当社の営業がお客さまに説明するときに,「高静圧ファンは通風抵抗が高めの装置に適していますよ」のような話が出てくるようになりました。
しかし,「通風抵抗」や「動作風量」をお客さまにイメージしてもらうのは難しいです。これらを見える化できる,お客さまのところへ持ち運びできるような装置は世の中には存在していなかったので,手探りで開発を始めたのですが,試作機が非常に好評で,製品化をすることになりました。
ファンメーカーはダブルチャンバー方式を採用しているメーカーが多いですね。一部,風洞測定装置を使用しているメーカーもあるようです。風洞測定装置は筒の中に圧力センサを2つ付けて,圧力差で風量を計算する仕組みです。
ファンの場合,大きい風量から小さい風量まで測定しますので,ノズル交換して,差圧を調整して,測定をおこなうダブルチャンバー方式のほうが適していると言われています。
あとは,風洞測定装置は動作風量しか測れませんが,ダブルチャンバーは最大風量と通風抵抗も測ることができます。
最大風量の測定条件はファンの周りに何もない状態ですが,風洞測定装置は筒状の風洞が必ず負荷になるため,最大風量を測ることはできません。ダブルチャンバー方式では補助ファンで風洞による損失圧力を調整するので,最大風量と同じ圧力0の状態にして測定できるのです。
それと,風洞装置には補助ファンが付いていないので,測定物が風を出さない装置の通風抵抗になると測れません。なので,基本的に風洞装置で測った風量-静圧特性カーブは,最大風量がなく,途中からスタートしたカーブになります。
今回開発したエアフローテスターの構造は,基本的にダブルチャンバー装置と同じです。
小さいものから大きいものまで,小さい風量から大きい風量まで,可搬で測定できるのがこのエアフローテスターの強みです。
ダブルチャンバー測定装置は大型で移動できません。通風抵抗に詳しいお客さまは,装置を貸すから測ってほしいと,装置を送ってくれる場合が多いですが,その場でしか測れない装置だと,今まではお断りせざるを得ない状況でした。
実際にはもっと,もっと前段階の話ですね。
そもそも通風抵抗や動作風量などの概念が,まだまだお客さまに浸透していないので,測ってみたいどころか知らないお客さまが大半です。そうなると,最適なファンを選定するには通風抵抗が必要ですとお客さまに言っても大体の反応は,「とりあえず良いファンをもってきて」「いっぱい風量出るものをもってきて」と言われますね。
例えば,モータなどを選定するときは,負荷やイナーシャを計算して選定しています。それがファンに関しては,風が目に見えないので,どのぐらい何の数値が必要なのかが分からないですね。
逆にある程度ご存知のお客さまのところに行くと,「こういう製品を待っていました」と言っていただけます。思ったよりニーズがありました。ある海外のメーカーのお客さまは,ファンの取り引きがなかったのに,広告をみて,わざわざ当社の工場まで電話をして,「これをずっと待っていたよ」と言ってくださったのです。
まあ反応はちょっと極端ですね。通風抵抗などに馴染みのないお客さまは,反応は薄いですね。エアフローテスターを使っても,今までの実機評価の工程が全部無くなるわけではないので,それでお金かけて何かメリットあるの,というところですかね。
エアフローテスターは選定のサポートツールとして,それぞれの工程を少しずつ短縮して,結果的に例えば開発期間を半分くらいに短縮できますよという効果になるので,装置の小型化などのシビアな課題を持っているお客さまでないと,なかなか共感いただけないですね。
構想は1年ぐらいで,基本的な実験,評価などをおこなって,実際この形にもってくるのは2年ぐらいかかりました。ファンの金型だったら,羽根とフレームだけ2~4型くらいで済みますが,エアフローテスターは全部で15型くらい作りました。いままでやったことがないので,全部手作業から始めます。最初に作った第1号機も今と全く違って変な形でしたよ。最初の目的は社内用のツールだったので,まず機能が満足できれば良いということで,第1号機は拡声器みたいな形でした。その後,製品化という話になって,デザインを見直すことになりました。
今までずっとファンを作ってきましたが,ファンの良し悪しは性能で決まりますし,電源を入れれば動作するもので操作性についてあまり意識していませんでした。しかし,エアフローテスターはファンと違って,お客さまがそのまま使う最終製品なので,デザインはもちろん,操作性も重視しようということで,何回も修正を重ねました。
プログラムの部分も一旦形にしないとよく分からないので,できるものを組んでから,みんなに触ってもらって,ブラッシュアップして作っていました。
このエアフローテスターは5代目か6代目ですかね。最終製品なので,性能をクリアした後の細かい修正に時間が掛かりました。製品に対するフィードバックもファンとは違って,お客さまにプレゼンした数,売れた数だけ戻ってきます。ずっとご要望を受けている状況なので,当分手が離れないかなと感じますね。
世の中になくて,お客さまの役に立つようなものを作りたいなといつも思っています。
これもファンとまったく違う分野ですが,お客さまのところに行って,いいねと言ってくれたときは,開発してよかったと思いますね。
自分はお客さまが困っていることを解決する仕事が好きですね。エアフローテスターみたいに,世の中にないものを形にできる立場にいるので,お客さまの悩みを解決できるといいなという思いで働いています。
エアフローテスターについて言えば,まだ概念のところが浸透していないので,セミナーをやって少しでも広がっていくといいなと思って,日々がんばっています。
今まで開発してきたファンは基本が確立しているので,こうしたほうが良いじゃないかという余地が少なかったのですが,今回エアフローテスターの操作部分の開発を担当して,今後もお客さまの目線で使いやすい製品にどんどんブラッシュアップしていきたいと思います。
この前,電気屋に自分が設計したファンが置いてあって,すごくうれしかったです。
実際に自分が作ったものを多く人に使ってもらうために,やったことがなくても,厳しい条件であっても,負けずにこれからも開発を続けていきたいと思います。
更新日:/公開日: