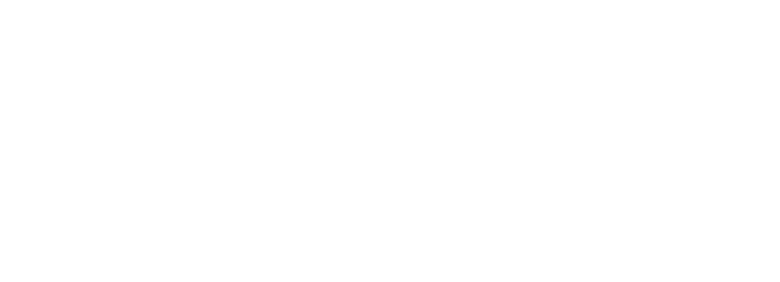
It has been some time since the "IoT of factories" such as smart factories and Industry 4.0 started to attract attention. Even in the field of "stable power supply," which is the lifeline of factory operation, the need for centralized monitoring by connecting UPS to a network is increasing year by year.
In this article, we will introduce the background to the growing need for centralized monitoring of UPSs and the question, "What are the actual benefits of centralized monitoring of UPSs?"
By connecting UPS to a network and installing monitoring software, it becomes possible to remotely monitor multiple UPSs from a single monitor. For example, it becomes possible to visualize statistical information such as the power supply status of the UPS, the occurrence of alerts, and the load factor. In addition to "monitoring," remote "control" such as shutting down the system is also possible, as described later.
There are several factors, but the main one is the increasing adoption of "edge computing" in the manufacturing industry.
As devices become more IoT-enabled, data volumes have increased dramatically in recent years. Manufacturing companies store this vast amount of data in the cloud and retrieve and process the data they need. Meanwhile, motion control, which performs high-precision machining, collects large amounts of data in extremely short periods of time, measured in milliseconds. If all of this data were sent to a host cloud, the communication and data volume load would be too great.
That's where edge computing comes in. See the diagram below.
When using cloud computing for the entire system, a large amount of data must be received and processed, which inevitably results in an excessively large "load" for data collection and processing. On the other hand, with edge computing, processing is performed at the edge in between, making it possible to collect and process data while "distributing the load."
The role of backing up each of these edge computers is provided by a UPS installed at each edge. For these reasons, factories are increasingly using multiple UPS devices, which is creating a growing need for centralized monitoring of the UPS devices.
When managing multiple UPS individually, you need to personally check the UPS scattered throughout a large factory. The same is true when performing power operations (such as shutting down) due to planned power outages. On the other hand, when monitoring UPSs collectively, you can remotely grasp the status of the UPS from a single monitor.
Maintenance work is already busy, so you want to minimize unnecessary travel as much as possible.
With UPSs installed all over the factory, battery maintenance is also a hassle. It is not uncommon to encounter situations like, "I replaced the battery here last month, but now it's time to replace the battery here..."
By monitoring multiple UPS devices at once, the battery status can also be visualized, making it possible to create a more or less comprehensive maintenance plan.
In addition, adopting a "lithium-ion battery UPS" is effective in reducing the hassle of battery maintenance. Please see the related columns below.
"Do you think lithium-ion batteries are expensive? Compare the battery life of UPS (Uninterruptible Power Supplies)!"
UPS can not only monitor but also control all of the equipment. Specifically, it can automatically shut down and start up computers (backed up by UPS). For example, centralized control is very useful not only during power outages and other power problems, but also during regular maintenance of factories.
If your factory has already introduced "IoT devices using Modbus communication" such as PLCs, you can easily connect the UPS to peripheral devices and monitor them all at once. *1
The UPS can be used as a Modbus communication master (parent device) to monitor and control slave devices, and vice versa. *1 If it can be connected to machine tools and production lines, it may be able to make a big contribution to "factory IoT" by visualizing data and analyzing accumulated data.
*1 When using a network card that supports Modbus communication, such as our LAN interface card.
To monitor multiple UPSs at once, a LAN interface card (LAN card) must be installed in each UPS and connected to the factory network.
Furthermore, to connect to other IoT devices in the factory, a network card that supports Modbus communication must be used.
We offer a lineup of LAN interface cards that are useful for centralized UPS monitoring, reducing maintenance man-hours, and implementing IoT in factories. We will introduce their main features.
Our LAN interface cards have both monitoring and shutdown functions. Therefore, there is no need to select a LAN card depending on the purpose (monitoring or shutdown), and they can be used for all purposes. They can not only monitor the UPS, but also control it.
Not only can it remotely "monitor" the power supply status and battery status, but it can also "control" functions such as shutdown and automatic startup, helping to significantly reduce maintenance labor.
Modbus is an open serial communications standard that allows seamless connection of devices from various manufacturers. It is widely adopted as the de facto standard in the industrial sector and is essential for the IoTization of factories.
Our LAN cards are compatible with Modbus, so they can be connected to Modbus-compatible peripheral devices and monitored all at once. In addition, the UPS can be used as the master (parent device) of Modbus communication to monitor and control slave (child) devices, and vice versa.
*For devices that can perform Modbus communication, please click here.
While many LAN cards only support wired connections, our LAN cards have a USB port, so by inserting a wireless adapter into the UPS, you can also connect to wireless Wi-Fi. This reduces the number of wires in factories with many wires, allowing for a neater installation.
Chemical manufacturer F (Number of employees: 5,000)
Chemical manufacturer F Co. has experienced multiple instantaneous drops in its factories due to the frequent torrential rains that have occurred in recent years, causing damage to its products and causing problems with recovery work. As a countermeasure, the company was considering introducing a UPS.
Mr. K, the maintenance manager, talks about his concerns at the time: "I thought it would be great if we could back up each of the three manufacturing lines in our factory with a single UPS, as it would be safe and easy to manage. However, when I got a quote, the cost of a large (high-capacity) UPS was so high that it was eye-wateringly expensive, and it was extremely difficult to secure the budget within the company."
After consulting with Mr. K, the sales representative from SANYO DENKI made the following suggestion: "In that case, why not install a UPS for each process, such as one for the inspection equipment and one for the labeler? The capacity of each UPS will be smaller, so although the number of units will increase, the total cost can be reduced."
"The fact that it would reduce costs was appealing, but managing 30 UPS units felt like a burden. The 30 units were used at different ambient temperatures, so the timing for battery replacement also varied. To be honest, I thought it would be a lot of work to maintain them every day," said Mr. K.
The SANYO DENKI sales representative then made the following suggestion: "How about using a LAN interface card to monitor all your UPS devices at once? You'll be able to see the status of all your UPS devices at once on a single monitor, and you'll also be able to plan battery replacements for a certain number of devices at once."
Mr. K was convinced by SANYO DENKI 's proposal and seriously considered and decided to install the SANUPS E11B UPS and LAN interface card. "I'm glad we installed the UPS. Since installing it, we've had a number of sudden downpours, but now we can operate the factory with peace of mind. Also, being able to monitor the UPS all at once has helped reduce the amount of maintenance work, which is very helpful. I'm very satisfied (Mr. K)."
Supervisor: SANYO DENKI CO., LTD. Sales Headquarters Power Systems Business Group
release date: