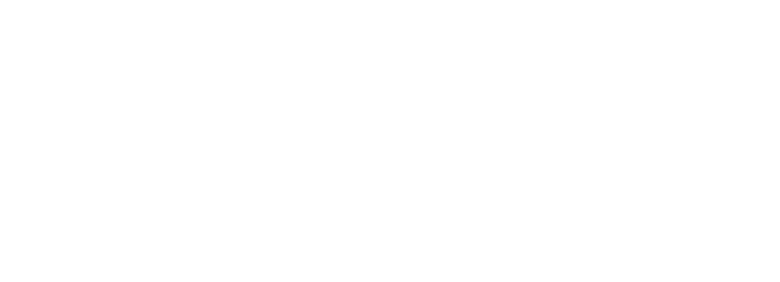
「溶接・接合」は,あらゆる産業において活用される必要不可欠な基盤技術です。近年,多くのメーカーが生産ライン効率化のために,溶接・接合工程の自動化を進めてきましたが,この工程は何よりも“品質確保”が求められます。また,溶接品質向上のためには,チップドレッサなどの周辺機械が必要となりますが,溶接時の作業スペース確保のため,周辺機械の小型化も同時に求められています。
溶接ロボットおよび周辺機械には高い信頼性が必要ですが,溶接機はノイズの発生源でもあり,周辺機械の誤作動や故障を引き起こしやすいという弱点を持っています。QA(品質保証)や安全性の観点から多くの改善すべき課題を抱えています。
C社は,金属接合の技術力を軸に,産業機械およびFAシステム関連製品の製造・販売を手掛けています。特に,アーク/スポット溶接ロボットと周辺機械の分野において,国内外のシェア拡大を狙っています。
同社では,溶接ロボットの周辺に設置される「チップドレッサ」において,ユーザーより寄せられたいくつかの課題を抱えていました。
そのひとつが“小型化”。チップドレッサは,溶接ガン先端の電極部を研磨し溶接精度を一定に保つ装置で,溶接ロボットには必ず装備されています。近年,製品開発の高度化・高速化とともに生産ラインが過密化するなかで,生産効率性の観点から,チップドレッサにも省スペース化が強く求められるようになっています。
その点,同社の現行モデルに採用されていたDD(ダイレクトドライブ)モータシステムでは,高効率,低騒音という大きなメリットを持つ一方で,クーラント液浸入によるモータ故障という問題を抱えていました。さらに,現行DDモータはモータ径が大きく,また,モータと溶接ロボット制御部とのセンサI/F(インタフェース)が違い,「センサ信号変換ボックス」が必要だったため,装置全体の大型化,かつコストが高くなるというマイナス面を払拭できずにいたのです。
そして二つ目の大きな課題は,TIGノイズに起因する装置の誤作動でシステムが止まり,生産ラインの稼働率が低下することでした。
溶接システムはその原理上,大電流が発生するため,極端にいえば“ノイズの元凶”であるともいえます。スポット溶接時には,この大電流とともにカットしにくいTIGノイズが発生し,このノイズをエンコーダやコントローラ,センサ信号変換ボックスが拾ってしまうことで,本来の波形出力に狂いが生じ,誤作動および故障を引き起こす原因になっていたのです。同社技術開発部 部長のA氏はこう語ります。
「不具合が頻発することで,工場の生産ラインに稼働率低下をもたらしている,という報告を受けて当社の技術者が検証したところ,既設モータシステムの信頼性に難があることがわかりました。チップドレッサには高精度の研磨能力と高い信頼性が求められるため,重大な改善要求として一刻も早く解決させる必要がありました。」
※TIG(ティグ)ノイズ:TIG溶接の際に発生するノイズ。TIG溶接とは,非溶極式のイナートガス溶接で,タングステンまたはタングステン合金を電極とする溶接。溶接材料に溶加棒を用い,電極が溶接材料とはならない非溶極式(非消耗電極式)のガスシールドアーク溶接。TIGは,Tungsten Inert Gasの略。
現行機の問題解決のため情報収集をおこなっていたA氏は,取引先からの紹介で山洋電気の営業担当と話す機会を持ちます。自社のチップドレッサが抱える問題について相談したA氏は,後日,現行のφ180mmDDモータによる構成を「80mm角ACサーボモータ+ギヤ」構成へ変更する提案を受けます。これはA氏にとってまさに「目からウロコの提案だった」といいます。
「目標としていたのは,100mm以内のサイズでしたが,提案していただいたACサーボモータ+ギヤは,80mm角でDDモータに比べても非常に小型なものでした。また,ロボットコントローラと同じI/Fのセンサを搭載したため,「変換ボックス」をなくすことができました。その結果,装置構成が簡略になり,さらに小型化できると期待が持てました。そのうえ,モータ本体においてIP67の保護等級に対応しており,クーラント液対策も向上する…言われてみれば,なぜ今まで気づかなかったのか不思議でした。」(前出A氏)
「センサ信号変換ボックス」をなくしたことは,二つ目の課題であった「ノイズ対策」にも有効でした。変換ボックスがTIGノイズを拾ってしまうことで,センサ波形が狂い,正しい信号を読み取れない要因となっていたので,そもそもの不具合発生の原因が取り除かれるのです。
「現行モデルではモータ軽量化のために樹脂製カバーを使用していましたが,ノイズ耐量の高い鉄製カバーの採用を提案いただきました。樹脂製と鉄製カバーの耐ノイズ評価の結果も提示いただき,向上していることが良くわかりました。また,ノイズ対策に最適な配線やノイズフィルタの設置など,ノウハウをいろいろと提案していただきました。」(前出A氏)
ほどなく,同社と山洋電気は試作機を製作し,評価試験を実施しました。約6ヶ月にわたる評価試験の結果,これまでの提案内容が理論値ではなく,現実値であることを確認するにいたります。
こうした検証を経て,C社は山洋電気製「高性能ACサーボモータ+ギヤ」を採用したチップドレッサの新モデル量産化を決定しました。A氏はこう総括します。
「山洋電気の提案は,ユーザーからの要求を満たし,装置性能を向上させるために欠かせないものでした。試作による評価期間は半年にわたり続きましたが,その間も山洋電気にはモータメーカーの枠を超え,柔軟な技術サポートをおこなっていただき大変ありがたく感じています。」
公開日: