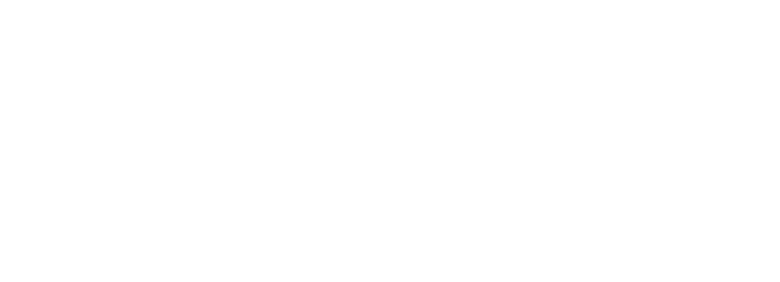
Company A is an industrial equipment manufacturer known for developing and manufacturing industrial robots. In recent years, the manufacturing industry has been facing fierce competition in terms of cost and quality, and there is an urgent need to further improve the efficiency of production lines. Company A is no exception, and users' demands for the performance of industrial robots are becoming increasingly higher day by day, putting a lot of pressure on developers.
Group Leader Y of the design group in Company A's development department had this to say:
"Six-axis vertical articulated robots, which have a structure similar to that of a human arm, are widely used along with horizontal articulated (SCARA) robots as the most rational devices for replacing humans in performing tasks. Our company has been involved in their development and manufacturing for a long time. However, users seeking a greater competitive advantage are increasingly calling for further improvements in terms of speed, size, and slimness, and frankly, we felt that we had reached a dead end in terms of further improvements."
Furthermore, the need to "shorten cycle time," an important requirement for efficient production lines, made development even more difficult. To speed up robot movements, a high-output motor is required, but high-output motors generally have a large mass. When used in a wrist mechanism, the moment of inertia on basic axes such as the main body's rotation axis increases, preventing speed increase. Increasing the size of the motor for the main body's rotation axis increases the installation area, making miniaturization impossible. In addition, increasing speed makes it difficult for the arm to turn corners, and it becomes necessary to slow down to maintain trajectory accuracy. Can the robot respond to this change in speed?
What further worried Mr. Y was how to reduce the settling time. Increasing the speed makes it easier for vibrations to occur at the tip of the arm, which has low rigidity. Even if the motor stops, that doesn't necessarily mean that the end effector, which is the hand part, is still. He knew that reducing this vibration was an essential element in shortening the cycle time. However, "We reviewed the entire structure to avoid putting a strain on the control system as much as possible, but with the current control system, we just couldn't reduce the vibration any further," said Mr. Y.
The common opinion of the development staff was that "it is difficult to meet the user's demands any further with the current control system." However, Mr. Y was not just sitting around doing nothing. He wanted to meet the user's demands by fundamentally reviewing something. This was a sincere feeling as an engineer.
The turning point for Mr. Y came when he was talking to a sales representative from SANYO DENKI, who was introduced to him by an engineer he knew. He was very intrigued by the information that "they have succeeded in developing a servo motor that is 30% smaller than conventional products and is the smallest in the industry*." Mr. Y immediately began testing it using a demo unit, and he was drawn to the various vibration control technologies that this servo system is equipped with.
*As of September 2006, according to our research.
"Despite being 30% smaller than previous models, both the maximum instantaneous torque and maximum rotation speed have been improved. It was perfect for our robots. We could achieve higher speeds without increasing the size of the motor. In fact, the reduced weight allowed us to completely rethink the structure of the robot, making it smaller and slimmer. It has raised our expectations for the evolution of robot performance, which had previously reached a plateau."
Another key point is that the high-resolution encoder, which has been improved from the previous 13 bit (8,192 divisions) to 17 bit (131,072 divisions), makes it possible to detect minute position deviations when the motor is stopped, and is expected to significantly improve trajectory accuracy and position repeatability.
The next thing Mr. Y verified was how to shorten the settling time. In this regard, the servo amplifier was equipped with advanced vibration control functions, including "feedforward vibration control" that is effective in suppressing vibration at the tip of the arm, and a "disturbance observer" that can minimize the effects of other axes.
This servo system, which uses advanced algorithms, is also excellent in terms of speed, and has succeeded in halving the settling time for positioning. This has paved the way for achieving both compactness and high speed, which are closely related, and shortening cycle times.
"We had predicted that increasing the torque would inevitably increase the installation space, but we were surprised to find that we could rethink the arm structure and make the entire robot more compact. If we can improve vibration control in addition to increasing the speed, we can achieve the synergistic effect of maximizing the robot's production efficiency and reducing the installation space." (Mr. Y)
After thorough verification, Mr. Y embarked on the development of a new 6-axis vertical articulated robot using the AC Servo Systems SANMOTION R on a trial basis. As a result, he succeeded in creating a prototype that fully met the user's needs.
The evolution of servo motors has made a major contribution to improving the performance of robots.
"Production sites have become increasingly diverse and complex in recent years, and I believe that industrial robots will be required to achieve even greater precision and performance in the future. This latest attempt has come a long way in meeting user needs, and we are currently working at a rapid pace to define requirements with a view to mass production in the future."
In a manufacturing industry that is experiencing rapid change, this is a good example of expanding the possibilities of industrial robots by addressing the major challenge of improving production line efficiency.
release date: