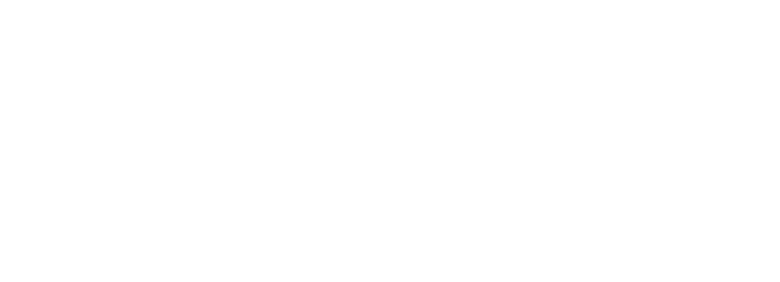
Company B, an industrial machinery manufacturer, was aiming to expand its share in the new automobile market, which was expanding due to the rise of eco-friendly cars such as hybrid cars and EVs. In particular, automation has been accelerating in Greater China in recent years to reduce labor costs. As this is a market expected to grow rapidly, Company B's success or failure in gaining market share will undoubtedly have a major impact on its future business. Under these circumstances, Company B also required a speedy component insertion machine for the manufacturing process of new circuit boards.
Company B needed to get results quickly in order to respond to changing market needs, so they considered reusing the current machine's applications to renew the system and shorten the development lead time. However, when they checked, they found that the program was written in the local language that was mainstream in Japan at the time because it was based on specifications from 10 years ago, and naturally the content was only understandable to the developers at the time.
Regarding this situation, Director S of the System Design Department at Company B said, "Software has changed rapidly over the past decade, and the industrial machinery that our company has developed up to now has been heavily dependent on individuals who were involved in its development during that time. Furthermore, many of the developers have left the company due to retirement or other reasons. The lack of sharing of in-house assets was a major blow."
Furthermore, problems arose regarding the system configuration. Because the drive system devices (controllers, servo motors, stepping motors, etc.) were optimized across multiple manufacturers, connecting the controller to devices from multiple manufacturers meant that the wiring was complicated, increasing not only the amount of work required for wiring the aircraft, but also the amount of work required for maintenance after delivery.
"These problems are preventing us from shortening development lead times. First of all, we needed to review our development environment from the ground up, including our disorganized internal assets." (Mr. S)
Mr. S consulted SANYO DENKI, which had a track record of introducing some of its servo system products, about these problems. As he spoke with the sales representative, he learned that many of these problems could be improved by using the company's controllers. Furthermore, SANYO DENKI not only provides equipment, but also undertakes contract development and provides technology to build optimal systems, and this support system also attracted Mr. S. Company B immediately decided to introduce SANYO DENKI 's Motion Controller" SANMOTION C"
Company B and SANYO DENKI first analyzed the application programs of the existing equipment and started by rewriting them in the PLC programming language (IEC61131-3) adopted by "SANMOTION C", which has been globally standardized by PLCopen. By using a standardized language, it became possible to share program content between engineers and to capitalize the software. In addition, when Company B develops derivative models, this structured programming makes it easier for them to work on the development of different equipment at the same time. This has resulted in a dramatic improvement in the efficiency of software development.
Company B's request for the renewal of its component insertion machine was to increase the number of component types from a maximum of 36 on the previous machine to a maximum of 48, and to improve the insertion speed and insertion accuracy. In response, SANYO DENKI proposed a system that collectively controls 11 servo motor axes and an 8-axis closed-loop Stepping Systems. In addition, the optimal combination was achieved through customization, and the needs of Company B were met.
In addition, "SANMOTION C" is available with a variety of field buses, including EtherCAT, which reduces wiring within the device, shortens assembly time, and improves maintainability.
Through various improvement measures, Company B succeeded in shortening development lead times by nearly 50%. They also achieved a 40% reduction in maintenance man-hours.
Mr. S summed up the renewal project as follows: "SANYO DENKI 's proposal was not just about the controller, but was optimal for the entire system. The designers responded directly to technical inquiries, which allowed for early resolution, and they always provided flexible support in line with our needs."
SANYO DENKI 's total solutions like these will continue to support Company B's new business ventures.
release date: