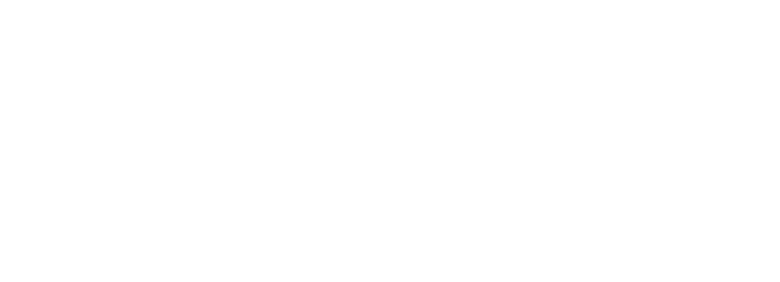
"Welding and joining" is an essential basic technology used in all industries. In recent years, many manufacturers have been automating the welding and joining process to improve production line efficiency, but this process requires "ensuring quality" above all else. In addition, peripheral machines such as tip dressers are required to improve welding quality, but at the same time, there is a demand to miniaturize peripheral machines in order to secure working space during welding.
Welding robots and peripheral machines require high reliability, but welding machines are also a source of noise and have the weakness of easily causing malfunctions and breakdowns in peripheral machines. There are many issues that need to be improved from the perspective of QA (quality assurance) and safety.
Company C manufactures and sells industrial machinery and FA system-related products, with a focus on metal joining technology. In particular, the company aims to expand its market share both domestically and overseas in the fields of arc/spot welding robots and peripheral machinery.
The company had been facing several issues reported to them by users regarding the "tip dressers" that are installed around their welding robots.
One of these is "miniaturization." Tip dressers are devices that polish the electrode at the tip of a welding gun to maintain constant welding precision, and are always equipped on welding robots. In recent years, as product development has become more advanced and faster, and production lines have become more congested, there has been a strong demand for tip dressers to be more space-saving from the perspective of production efficiency.
In this regard, the DD (direct drive) motor system used in the company's current model had the great advantages of high efficiency and low noise, but it had the problem of motor failure due to coolant seeping in. Furthermore, the current DD motor had a large motor diameter, and the sensor I/F (interface) between the motor and the welding robot control unit was different, requiring a "sensor signal conversion box," which resulted in the overall equipment becoming larger and the costs becoming higher, which could not be eliminated.
The second major issue was that TIG noise caused equipment malfunctions, which would stop the system and reduce the operating rate of the production line.
In principle, welding systems generate large currents, so to put it bluntly, they can be said to be the "source of noise." When spot welding, this large current generates TIG noise that is difficult to cut off, and this noise is picked up by the encoder, controller, and sensor signal conversion box, causing distortion in the original waveform output, leading to malfunctions and breakdowns. Mr. A, head of the company's Technology Development Department, said the following.
"We received a report that frequent malfunctions were causing a drop in the operating rate of the factory's production line, and our engineers investigated the issue and found that there was a problem with the reliability of the existing motor system. Because tip dressers require high-precision polishing capabilities and high reliability, this was a major improvement request that needed to be resolved as soon as possible."
*TIG noise: Noise generated during TIG welding. TIG welding is a non-consumable inert gas welding method that uses tungsten or a tungsten alloy as the electrode. It is a non-consumable (non-consumable electrode) gas-shielded arc welding method that uses a filler rod as the welding material and the electrode is not the welding material. TIG is an abbreviation for Tungsten Inert Gas.
Mr. A, who had been gathering information to solve the problems with the current machine, had the opportunity to speak with a sales representative from SANYO DENKI through a client's introduction. After consulting about the problems with his company's tip dresser, Mr. A later received a proposal to change the current φ180mm DD motor configuration to an "80mm square AC servo motor + gear" configuration. This was a truly "eye-opening proposal" for Mr. A.
"Our goal was to have a size of less than 100mm, but the proposed AC servo motor + gear was 80mm square, which was extremely small even compared to a DD motor. Also, because it was equipped with a sensor with the same interface as the robot controller, we were able to eliminate the 'conversion box.' This has simplified the device configuration, and we expect it to become even more compact. What's more, the motor itself has an IP67 protection rating, which improves protection against coolant... Now that you mention it, it's strange why we hadn't noticed this before." (Mr. A, mentioned above)
Eliminating the "sensor signal conversion box" was also effective in solving the second problem, "noise countermeasures." The conversion box picks up TIG noise, which distorts the sensor waveform and makes it impossible to read the correct signal, so the original cause of the problem was eliminated.
"In the current model, we use a plastic cover to reduce the motor weight, but they suggested using an iron cover, which has higher noise resistance. They also showed us the results of a noise resistance evaluation of the plastic and iron covers, and it was clear that there was an improvement. They also suggested a variety of know-how, such as optimal wiring for noise countermeasures and the installation of noise filters." (Mr. A, mentioned above)
Shortly after, the company and SANYO DENKI produced a prototype and conducted evaluation tests. After about six months of evaluation tests, they confirmed that the previous proposals were not theoretical values, but realistic values.
After going through these tests, Company C decided to mass-produce a new model of tip dresser that uses SANYO DENKI Denki's "high-performance AC servo motor + gear." Mr. A sums it up as follows:
"SANYO DENKI 's proposals were essential for satisfying user requirements and improving equipment performance. The prototype evaluation period lasted six months, but even during that time SANYO DENKI went beyond the boundaries of a motor manufacturer and provided us with flexible technical support, for which we are extremely grateful."
release date: