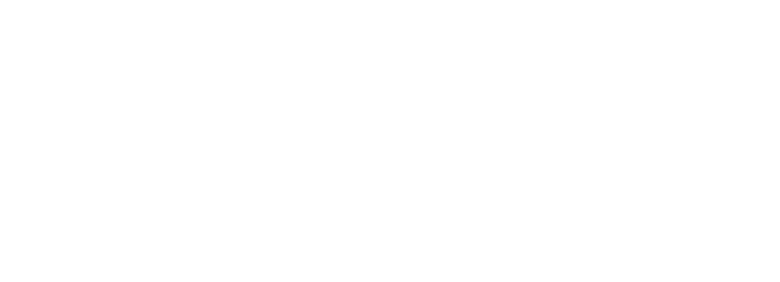
Automobile and electronics manufacturers are working harder than ever to improve quality. Parts manufacturers and other partner companies are also proactively introducing precision measuring instruments into their production lines as a way to improve product quality without manual intervention.
Against this background, the measuring equipment market has been expanding in recent years. However, the demands for "high accuracy," "high reliability," "compactness," and of course "low price" are becoming increasingly strict, and the competition between measuring equipment manufacturers is becoming more intense.
Company E, which develops and manufactures various types of measuring equipment, launched a development project for a small precision measuring machine for integration into production lines in order to strengthen its competitiveness.
Mr. M, development manager at Company E, had this to say:
"Precision measuring instruments are being introduced not only in departments such as research and development and quality control, but also at production sites. What is needed here is high-quality measuring instruments that can take stable, highly accurate measurements even in production sites where the temperature changes drastically. There is also a demand for compact, low-cost instruments that can be installed in-line at production sites."
As applications and uses expand, new technical challenges are also arising.
"When you build a power system using the 200V AC power supply used in factories, the control equipment inevitably becomes large. The parts are also large and expensive. Furthermore, when using high voltage, the safety standards are strict, which is an obstacle to miniaturization.
So we decided to configure the power system to be DC 48V or less. We thought that this would enable us to significantly reduce the size and cost of the control equipment. Also, to make the equipment more compact, we decided to in-house manufacture servo amplifiers with a shape that would fit into the available space in the equipment." (Mr. M)
Having decided on a policy of miniaturization and cost reduction, Company E began searching for the optimal servo motor.
We conducted repeated tests to find a motor that could be operated at DC 48V or less, but...
"Because we lowered the voltage, we had to increase the current passing through the motor to achieve the same rotation speed. Also, in order to make the device more compact, we decided to downsize the motor from the 73 mm square that was used in previous models. This resulted in more heat being generated by the motor. Heat causes metal to expand thermally, resulting in errors in measurements. The motor is used in an environment with drastic temperature changes, and to ensure measurement accuracy, we had to keep heat generation to a minimum, but no matter which manufacturer's motor we tried, the tolerance was far exceeded." (Mr. M)
Development was reaching a deadlock, and Mr. M was troubled by the difficult task of combining miniaturization with high precision.
Searching for a solution, Mr. M contacted a sales representative at SANYO DENKI, a manufacturer of DC Servo Systems, to discuss these issues. He was then advised to "customize and optimize the DC servo motor," and immediately asked them to help him.
Shortly after, SANYO DENKI delivered a prototype with customized winding specifications to meet the requirements of Company E. Upon receiving the motor, Company E immediately began installing it in an actual machine and conducting testing.
"This device uses a three-axis DC motor, and they designed a motor that could produce the exact speed and torque required for all three axes. I was amazed at their high level of expertise and technical skill in fine-tuning the windings.
However, the temperature of the Y-axis exceeded the allowable limit slightly. Because the load was inefficient, it was necessary to increase the current to achieve the target rotation speed, which inevitably resulted in a large amount of heat generation. Since the motor capacity could not be increased due to limitations in the mounting area, we decided to improve the structure around the load.
"A motor designer from SANYO DENKI then worked with us to think about the heat generation problem, examining the heat dissipation path and air flow, and gave us advice. I was pleased with their kind attitude of working with us to solve the problem," said Mr. M.
By fine-tuning the winding specifications and improving the heat dissipation efficiency of the motor on the machine side, they succeeded in reducing the motor surface temperature by more than 10°C. When they were able to keep heat generation within the allowable range, Mr. M was convinced that they could achieve both miniaturization and high precision in the device.
Furthermore, SANYO DENKI proposed customizing the motor shaft so that the pulley from the previous machine could be reused. This detailed support was the deciding factor in E's decision to adopt SANYO DENKI 's DC servo motor.
"This time, we thought we could use a small-capacity DC servo motor, which has high responsiveness at low speeds, and manufacture the amplifier in-house to make the device more accurate, more compact, and less costly, but we ran into an unexpected obstacle: heat generation. However, by resolving these issues, we were able to use a DC servo motor and successfully reduce the installation space of the measuring machine by 40%. We also found that by manufacturing the amplifier in-house, we could eliminate unnecessary functions and reduce costs by 30%." (Mr. M)
A few months later, after successfully completing the development of the measuring device, Mr. M had this to say:
"I feel relieved that we were able to achieve our development goal, which had almost reached an impasse. I am very grateful for the detailed customization, as well as the consideration given to costs. I will definitely consult with SANYO DENKI first if I encounter any difficult issues in the future."
release date: