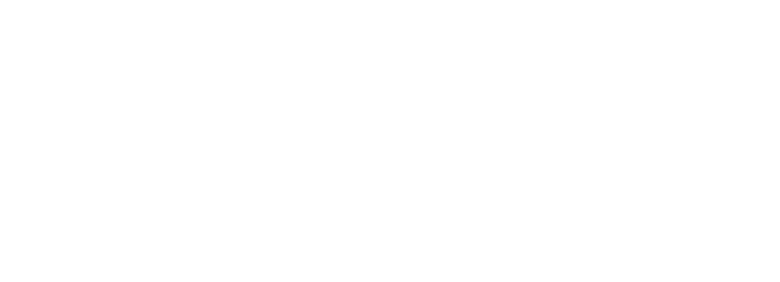
Company T, a developer and manufacturer of 3D printers, had been focusing on the development of high-end 3D printers in anticipation of market expansion. Mr. U, a group leader of the design department, said, "We were looking for a 3D printer that could be used in a wide range of applications.
The 3D printer market has been booming in recent years," said Dr. Gerhard Schmidt, CEO of the 3D Printer Association of America, "and with the expiration of the FDM (thermal dissolution lamination)* patent in 2009 and the SLS (powder sintering)* patent, which is common in high-end 3D printers, in 2014, more and more manufacturers are entering the market.
In the U.S., a grant program has been established to promote research and development of 3D printers, and a similar grant program will be established in Europe. As a result, the market is expected to continue to grow.
* FDM (Fused Deposition Modeling): Thermal melting and laminating method. A three-dimensional shape is created by melting and layering resins at high temperatures.
* SLS (Selective Laser Sintering): Powder sintering method. SLS (Selective Laser Sintering): Sintering of resin or metal powder by laser irradiation.
Because of its ability to significantly reduce the product prototyping and evaluation process, Company T was working daily to develop a 3D printer that would help users shorten their development time and increase their competitiveness.
Accuracy in 3D printers is based on the smooth movement of the X-Y axes and the synchronization of nozzle opening and closing. In the current machine, we had configured a servo system with a PLC and pulse train I/O to mechanically improve the accuracy, but that too was at its limit. In order to achieve precise, high-quality modeling, we were considering adopting a gantry structure instead of the conventional single actuator for each of the X and Y axes, but this required a servo system with higher synchronization performance and lower vibration than ever before. (Mr. U)
We were also faced with the challenge of increasing speed.
We wanted to shorten the cycle time by increasing the molding speed. However, if we simply tried to increase the speed, vibration would occur during acceleration and deceleration. We could not afford to compromise molding quality.
We also wanted to increase the molding space without changing the size of the machine from the current model in order to differentiate ourselves from our competitors. (Mr. U)
The challenges piled up: how to achieve high-quality, high-density, high-definition modeling in a shorter period of time?
Mr. U visited an exhibition to find a solution, and consulted with SANYO DENKI about these issues. Later, a SANYO DENKI sales representative visited Company T and, after confirming the detailed requirements, proposed the "SANMOTION R ADVANCED MODEL," AC Servo Systems equipped with an EtherCAT interface.
"AC Servo Systems proposed to us was based on the open network EtherCAT communication specifications. EtherCAT has a high-speed communication cycle of up to 0.125 msec, so position commands can be subdivided, making the equipment operate smoothly. In addition, the position feedback synchronization function improves the controllability of multi-axis synchronization. Furthermore, the jerk profile function reduces vibration during acceleration, deceleration and stopping, improving positioning accuracy. We are also looking forward to shortening the tact time." (Mr. U)
Company T immediately decided to evaluate the head unit on an actual machine.
After evaluation, we succeeded in improving the accuracy of the head unit by 30%. We were convinced that we could achieve high-speed, high-definition modeling. Also, the drive unit is smaller than that of the current model, so we succeeded in increasing the molding space by 15% while maintaining the same size as the current model. (Mr. U)
Mr. U also talks about future developments.
"Due to the transmission speed of EtherCAT communications and the flexibility of the connection method, we are considering developing a model that can connect to several 3D printers with one master controller and print different parts simultaneously, if there is future customer need. The model we developed this time was a top-of-the-line model, but personal use is also spreading in the market. SANYO DENKI has a diverse lineup, including a closed-loop Stepping Systems and a DC 48V input AC Servo Systems that are ideal for the high-end model for personal use that we are planning to develop in the future. We look forward to seeing more proposals from SANYO DENKI in the future."
Published On: 00