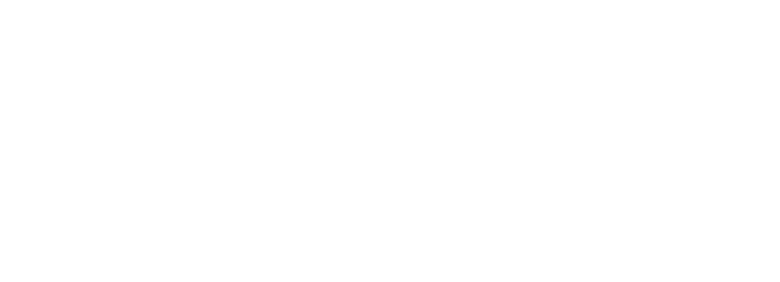
Company B, a food handling equipment manufacturer, was working on developing a new automatic sorting device. The new product was going to use a servo motor, and Mr. S from the development department proceeded with the development in a trial-and-error manner.
"There is a high need for automation in the food industry, and equipment is always required to improve its cycle time. At the same time, cost is important, so when positioning is required, we use stepping motors, which have cost benefits. However, because this new product handles large ingredients, we decided to use a servo motor, which has high torque. We have accumulated know-how from our experience working with stepping motors up to now, but we had little experience working with servo motors, so we didn't have anyone in charge of development who was knowledgeable about them," said Mr. S.
After much trial and error, he completed a prototype device, but he wasn't sure if he had selected the right motor, so he asked a motor manufacturer for advice.
"Since this new product only sorts food, it does not require complex movements. Using servo motors increases costs, but we wanted to build an inexpensive system by eliminating unnecessary functions as much as possible. Also, because this is a device that handles food, it needs to be washed, so waterproofing of the motor was also a must.
So we asked the manufacturer of the motor that was installed in the prototype device for advice, but they only told us what was in the catalog... We were in trouble." (Mr. S)
During a meeting with a SANYO DENKI representative, with whom Mr. S had a business relationship on other equipment, he brought up the topic of a product under development, and the representative pointed out the possibility that the product was over-specified.
"When selecting a stepping motor, we always ensure a torque margin of about twice the normal torque to prevent loss of synchronization. We also ensured a torque margin when selecting a servo motor this time. However, the SANYO DENKI representative told us that because servo motors do not require a torque margin, there was a possibility that the motor might be over-specified." (Mr. S)
Mr. S decided to explain the equipment specifications in detail to the SANYO DENKI representative and ask for their assistance in making the selection.
Later, a SANYO DENKI engineer measured the torque using Company B's prototype device.
"After the measurements, we found that it was indeed over-specified. So, based on the results of the measurements, SANYO DENKI suggested reducing the motor capacity from 1.5kW to 1.2kW," says Mr. S.
SANYO DENKI also calculated the required motor rotation speed from the load speed and proposed the optimal amplifier.
"Once we knew the required motor rotation speed, we changed the gear ratio with the load from 1/17 to 1/15, which reduced the motor's maximum rotation speed. By doing so, we were able to change the amplifier capacity from 50A to 30A, achieving an overall cost reduction. In addition, SANYO DENKI 's servo motors come standard with IP65(*) waterproof performance, so there were no problems with cleaning the equipment. Thanks to their accurate support, we were able to make up for delays in development." (Mr. S)
In the future, Company B plans to actively expand the use of servo motors across its business.
*Protection rating IP65
Dustproof: Dust cannot penetrate the inside / Waterproof: Not adversely affected by direct water jets from any direction (according to IEC60529)
release date: