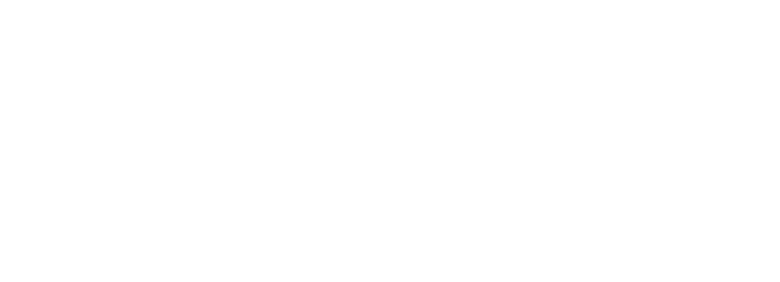
Company C, an automobile parts manufacturer, operates production equipment equipped with a large number of servo motors in its factory.
The company was considering replacing the DC servo motor that it had been using for many years with one that was to be discontinued. However, after looking at motors from several manufacturers, they found that there were no motors on the market that matched the size of their existing equipment. Mr. D from the Development Department at Company C said:
"The existing motor was an old design and had different dimensions from the current model, so in order to fit the new motor we needed to make significant modifications, including rebuilding the drive section. However, we had received instructions from higher-ups to keep the budget as low as possible, so we were in a situation where we couldn't make any major modifications," said D.
In addition, motors and electronic components are required to have high environmental resistance.
"At our factory, the dust and mist generated during the manufacturing process was causing early damage to electronic components, so we needed environmental resistance not only for the motors but also for the amplifiers," said D.
Furthermore, Company C operates its business not only domestically but also globally.
"This equipment is used in factories all over the world, so we had to replace a considerable number of pieces. We needed to keep the replacement cost per piece of equipment as low as possible," said D.
Mr. D, who was having trouble selecting a servo motor, was introduced to SANYO DENKI by a trading company with which he had a track record of doing business. SANYO DENKI 's staff listened to Mr. D's concerns and then proposed the AC servo motor "SANMOTION R" They also proposed customizing the motor shaft shape so that it could be used with Company C's existing equipment.
"We were told that retrofitting would be possible without changing the existing equipment, just by modifying the shaft. SANYO DENKI was the only company that could offer such a custom-made solution." (Mr. D)
SANYO DENKI 's staff also considered measures to deal with the issues of dust and mist. They found that no measures were necessary because the motor has IP65 certification as standard. However, measures were necessary for the amplifier that sends power to the motor, and they learned that environmental resistance could be improved by applying a special coating to the multiple circuit boards mounted on the amplifier. Mr. D was hopeful that this proposal would be able to withstand the factory environment.
SANYO DENKI continued to meet with Mr. D and made various proposals to address the issues.
"SANYO DENKI 's technical support team calculated the necessary torque based on the operating conditions of the actual machine and selected a new motor. As a result, we found that by customizing the windings, we could reduce the amplifier capacity by one level. This was an important suggestion that led to reduced replacement costs.
Furthermore, SANYO DENKI 's battery-less absolute sensor-embedded servo motors are proposed with the expectation of secondary benefits, such as making it easier to restart in the event of a power outage, and changing DC servo motors, which require periodic brush replacement, to AC servo motors, which are maintenance-free." (Mr. D)
Having recognized these benefits, Mr. D decided to officially adopt SANYO DENKI 's servo motor "SANMOTION R" and immediately replaced his equipment.
"In the end, we were able to replace the existing motor and amplifier with new ones without changing the operability or interface of the existing equipment. What's more, the amount of work required for the replacement was also significantly less than initially expected.
We plan to expand to factories around the world in the future, so we look forward to continued support from SANYO DENKI." (Mr. D)
release date: