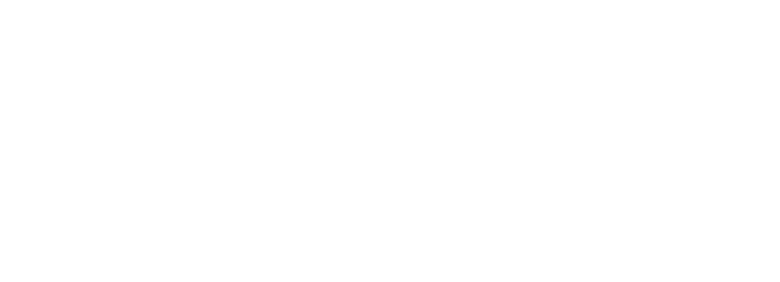
Company A is an equipment manufacturer that manufactures and sells automated assembly equipment for a variety of industries, and recently made some improvements to its production facilities. Mr. B, a production technology manager at Company A, explains:
"The first issue was traceability. Our company has been working on various improvements to control quality up until now. However, as equipment becomes more sophisticated, the number of parts increases and work processes become more complex. In this environment, we have started to see cases where issues such as improper screw tightening have affected the quality of the equipment.
To thoroughly manage this, we need to go as far as to ensure traceability of screw tightening. We were not able to do this with our previous production equipment, so we decided to make improvements this time. Improvement in this area was urgently needed.
The second issue was how to make the equipment smaller and lighter, and how to shorten the cycle time, which were also cited as important points for improving production efficiency.
"To achieve this, we needed to make the motor smaller and significantly faster. However, because a motor rotating at high speeds has a significant impact on the surrounding components, we needed to take adequate measures to protect it from shocks," said Mr. B.
Despite anticipating technical hurdles like these, Mr. B and his colleagues continued to gather information in search of a solution.
Mr. B consulted with SANYO DENKI, who had a track record with the company in other projects, about these issues. The SANYO DENKI representative recommended the servo motor "SANMOTION R" (flange size 20mm square) to Mr. B.
"Servomotors can output the torque value for each screw that is tightened, so by storing the data in an external device, it is possible to quickly identify problematic parts if an error occurs during manufacturing. As well as ensuring thorough traceability, this can also be applied in the future to predict failures and create smart factories using the IoT.
In addition, the proposed motor with a 20mm square flange size is expected to contribute greatly to making the device smaller and lighter." (Mr. B)
However, after looking at the motor specifications, Mr. B expressed reservations, as the standard maximum rotation speed (rpm) was not enough to achieve the cycle time reduction that Company A was looking for.
"This motor was characterized by its small size and high torque, but its maximum rotation speed did not meet the specifications we required. When we pointed this out, the person in charge further examined the usage conditions and made an additional proposal that it was quite possible to increase the rotation speed." (Mr. B)
SANYO DENKI continued durability testing and verification while holding multiple technical meetings with Mr. B and others, and customized the motor to increase its maximum rotation speed. Furthermore, by reviewing the operating pattern, the load on the motor was reduced, achieving the target value.
"SANYO DENKI didn't just stick to catalog specifications, but instead provided technical support that was tailored to our usage conditions. This kind of custom proposal is something that no other company offers, and thanks to them we were able to achieve performance that exceeded our expectations. We look forward to continuing to consult with them on various matters." (Mr. B)
release date: