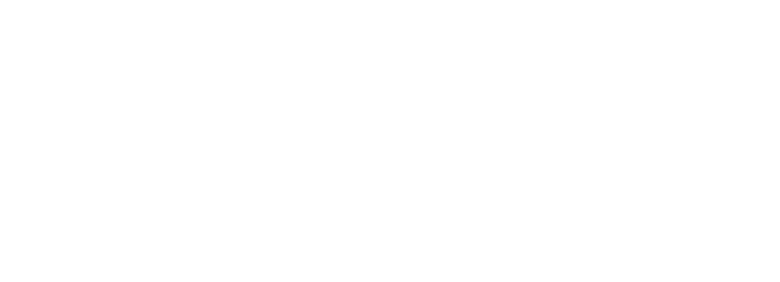
![]() |
Sanyo SANYO DENKI CO., LTD. Kangawa Factory [Site area]67,140m2 [Number of employees] 648 [Certification] ISO9001, ISO14001 We have installed a large-scale automated production line and carry out integrated production of servo system motors. |
▲Disk module for encoder (image)
Based on its medium-term management plan, SANYO DENKI is currently building a "production innovation line" aimed at strengthening automation in its own factories.
The Kamikawa Factory (Nagano Prefecture), which carries out integrated production of servo motors, was working on automating the assembly process of disk modules for encoders. Suzuki from the Production Technology Department explains:
"The goals of the Production Innovation Line were extremely challenging, including not only precisely achieving the performance targets set at the time of design and stabilizing quality, but also cutting production man-hours in half and lead times by a quarter. As part of achieving these goals, we focused on the labor-intensive and time-consuming assembly work of encoder disk modules and considered automating this task. Assembling encoder disk modules requires skilled techniques, so the challenge began." (Suzuki)
"Some people suggested that it would be more efficient to outsource to an external equipment manufacturer, but we decided that assembling the highly accurate disks would not be possible with commercially available equipment, so we decided to manufacture the assembly equipment in-house. The benefits of in-house production were great, including reduced manufacturing costs and a stable supply, and above all, the enthusiasm within the company to take on the challenge of future developments was what pushed us to develop it ourselves." (Suzuki)
Shortly after, the Production Technology Department began developing an assembly machine for disk modules for encoders. However, there were many challenges to overcome, such as how to reproduce the high-precision positioning achieved by skilled workers with a motor.
▲Disk module for encoder (image)
The encoder disk module assembly equipment that the Production Technology Department was developing had several processes in which highly precise positioning was essential.
"One of these was the process of precisely aligning the central axis of the hub and the central axis of the disk. A camera is used to recognize minute errors in the pattern printed on the disk, and any misalignment detected is corrected during assembly. Until now, this was a task that was done visually with a microscope, and it is a process that requires skill on the order of microns. A high-resolution motor is essential for determining the correct position, and high-precision motor control is also necessary to enable the dispenser to apply adhesive to the desired location." (Suzuki)
▼Disk module component configuration
Therefore, we incorporated the AC servo motor "SANMOTION G" that we are currently developing in-house, and completed the encoder disk module assembly device.
▼Completed encoder disk module assembly device
Equipment overview:
The process from disk module assembly to inspection has been automated.
Servo axis configuration:
The encoder of the servo motor "SANMOTION G" currently under development is 23-bit as standard *1, enabling 64 times finer positioning precision than our previous products.
*1 23-bit is the precision that enables positioning to within approximately 1/8.3 million angle per rotation.
In addition, the newly developed current control improves the speed frequency response from 2.2 kHz to 3.5 kHz, allowing for quicker response and operation than before, leading to improved machining quality.
"By using this motor, we were able to achieve more precise positioning. By combining this with image processing and correcting minute misalignments, we were able to achieve highly accurate adhesive application by the dispenser." (Suzuki)
This assembly equipment has significantly reduced cycle time and ensured a stable supply of disks. Having achieved this innovative production line, the Production Technology Department is determined to continue taking on new challenges with the manufacture of the next automated assembly equipment.
release date: