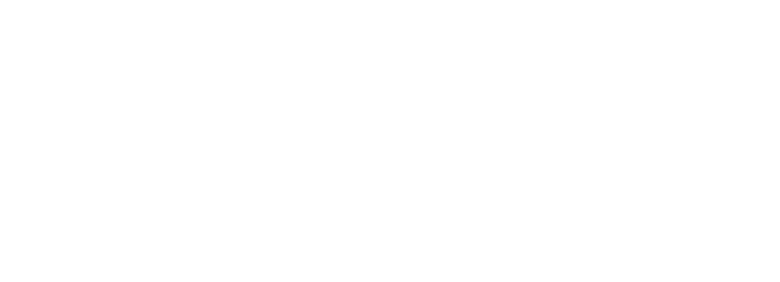
Are you able to prevent sudden breakdowns in your factory equipment? The impact of sudden breakdowns in factory machinery and other equipment is not just repair costs. If the production line stops during the repair period, production will be delayed, leading to the loss of profits that would have been gained during the line downtime.
So how can we prevent sudden breakdowns? Maintenance is essential for this purpose. In this article, we will explain what types and methods of maintenance are available, why predictive maintenance has recently become important in many companies, and why predictive maintenance that detects signs of motor failure is important in factories.
Predictive maintenance involves constantly monitoring factory machinery and other equipment to determine the state of deterioration of parts and, when signs of an impending breakdown are detected, carrying out maintenance work such as replacing or repairing parts before the machinery or equipment actually breaks down.
In preventive maintenance, maintenance work is carried out in a planned manner based on information provided in advance by the machinery manufacturer, such as "This machine requires maintenance every five years."
It is similar to the predictive maintenance mentioned above in that it involves performing maintenance work before a breakdown occurs, but the difference is that it is maintenance work that is planned from the start.
Corrective maintenance, as the name suggests, is maintenance work carried out after a breakdown has occurred. In order to minimize the period during which the production line is down, it is necessary to determine the cause of the breakdown and carry out repair work as quickly as possible.
However, while preventive maintenance would have been enough to simply replace the parts, corrective maintenance requires a larger scope of work and the costs tend to rise. Also, if the parts are not in stock, the production line will stop until the parts arrive, which will result in costs and a large loss of profits.
The impact of sudden breakdowns in factory machinery and other equipment goes beyond repair costs. Generally, production sites are required to produce at a high operating rate based on production plans.
However, repairs due to breakdowns cause the production line to stop, resulting in downtime, which can lead to production delays and loss of profits that would have been gained during the downtime. For this reason, how to prevent breakdowns has long been an issue on the ground.
As mentioned above, corrective maintenance is based on the idea of "repairing something if it breaks," and is not intended to prevent something from happening in the first place.
"Preventive maintenance," which involves making a plan and performing regular maintenance, is a method that has been used for a long time, and by thoroughly carrying out maintenance according to the plan, it is possible to reduce the possibility of breakdowns to some extent.
However, it is possible that a part may go wrong after regular replacement, and preventive maintenance cannot completely prevent such cases.
Furthermore, with preventive maintenance, there is a tendency to increase the frequency of maintenance in an attempt to reduce the possibility of breakdowns even just a little.
Increasing the frequency of maintenance will result in parts having to be replaced even though they are still usable, which will increase the cost of replacement parts and labor costs.
Predictive maintenance involves constantly monitoring factory machinery and other equipment, and when a certain level of deterioration or change occurs in a part, it is considered a sign of an impending breakdown and maintenance work is carried out.
Therefore, there is no need to replace all parts that are still usable just because it is a periodic replacement like preventive maintenance. It is possible to keep the cost of parts and replacement work to a minimum when replacement is necessary, which can also reduce costs.
Even if regular replacement is performed as part of preventive maintenance, deterioration or malfunction may occur at some point before the next replacement is due.
With predictive maintenance, abnormalities can be detected by constantly monitoring waveforms such as vibrations, allowing maintenance work to be carried out, increasing the likelihood of preventing breakdowns.
The disadvantage is that building a monitoring system such as IoT/AI requires construction costs.
In this regard, it is necessary to organize the risks of breakdowns into categories such as corrective maintenance for things that can be repaired when they break, and predictive maintenance for risks that need to be prevented as much as possible, and then calculate appropriate costs and estimate the cost-effectiveness.
Generally, to perform predictive maintenance, it is first necessary to attach IoT sensors to the equipment to be monitored in order to collect necessary information such as vibration and temperature.
You also need a system to collect and analyze the data from the sensors. After that, you need to repeatedly make hypotheses and verify which values in each piece of data are signs of anomalies, and find the optimal values.
Servo motors, which are essential for high-precision positioning and rotation control, are used in factory equipment in a wide variety of industries. Therefore, proper predictive maintenance of servo motors is extremely important for the stable operation of factories.
If you want to prevent servo motor failures, one option is to use a servo motor amplifier with predictive maintenance functions.
Motors and amplifiers with predictive maintenance functions are equipped with functions such as predicting the remaining life of holding brakes, monitoring overvoltage warning and frequency of the control power supply, monitoring the main circuit power supply quality, monitoring the upper level communication quality (EtherCAT), and monitoring the encoder communication quality, making it possible to identify factors that may cause failures in servo systems and equipment.
In addition, part life notification can help eliminate downtime for machinery and equipment.
Here we will introduce the features of SANYO DENKI 's AC AC Servo Systems AC Servo Systems" SANMOTION G"
The encoder is equipped with a full range of functions to ensure safe and secure use, including power supply status and communication quality monitoring, holding brake life prediction, and electronic component failure prevention. In addition, the encoder is battery-less, eliminating the need for battery replacement. This improves the reliability and maintainability of machinery and equipment.
It provides powerful control of equipment with high speed and high precision, contributing to improved equipment productivity and processing quality. Compared to our previous model *1, the following servo performance has been improved.
*1: Compared to our previous servo system, SANMOTION R
*2: The frequency indicates how stably the motor can follow the speed command from the servo amplifier.
The vibration resistance of the servo motor has been doubled compared to our previous model *3, and the servo amplifier has been improved by 20%. The operating temperature range of the servo amplifier has been expanded by approximately 10% to 0 to +60°C. It can also be used at altitudes of up to 2,000m. With improved environmental resistance, it can be used in a variety of regions and environments.
*3: Compared to our previous servo system, SANMOTION R
So far, we have introduced an overview of predictive maintenance and how to achieve it.
Predictive maintenance is already commonplace in a variety of industries, including manufacturing, energy, and healthcare, and is expected to spread to even more fields in the future.
Company T manufactures and sells equipment such as mixers that mix raw materials for food, chemicals, etc.
One of the company's customers, a food manufacturer, was suffering from the damage caused by downtime due to equipment failure.
When the equipment stops, the products being produced are discarded and the line cannot be restarted until the cause is identified, which has a huge impact on productivity and profitability. The food manufacturer has drawn up a new maintenance plan and asked T Company to develop a mixer that can perform predictive maintenance. However, the cost requirements are strict...
In a difficult position, Company T consulted with a sales representative from SANYO DENKI with whom they had a business relationship.
After listening to the customer's issues, SANYO DENKI determined that most serious failures with this mixer were caused by the motor, and proposed AC Servo Systems" SANMOTION G"
Being able to detect factors that could cause serious failures in advance has improved the accuracy of predictive maintenance and reduced the risk of downtime, which is a key factor in planning production.
Supervisor: SANYO DENKI CO., LTD. Sales Headquarters Servo System Business Group
Update date: /release date: