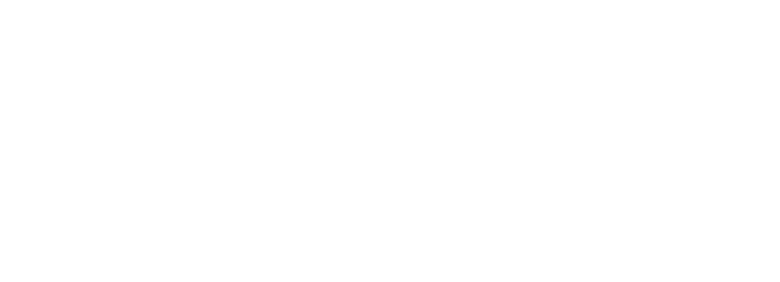
装置メーカーのA社。同社では多様な業種に向けた自動組み立て装置の製造販売を手掛けていますが,このほど自社の生産設備について,いくつかの改善をはかっていました。A社生産技術担当のB氏はこう説明します。
「1つ目の課題はトレーサビリティでした。当社では,これまで品質管理のため,さまざまな改善に取り組んできました。ですが,装置が高性能化していくなかで,部品点数が増え,作業工程も複雑になっています。そのようななか,ネジ締めの不良などが装置の品質に影響を与えるような事例が出てきました。
それを管理徹底するためには,ネジ締めのトレーサビリティまで踏み込む必要があります。いままでの生産設備ではそこまでできなかったので,今回改善することにしました。この点の改善は急務でした。」
また,2つ目の課題として,装置の小型・軽量化やサイクルタイム短縮も,生産効率向上のための重要なポイントとして挙げられました。
「これらを実現するためにはモータの小型化とともに大幅な高速化が求められました。しかし,高速で回転するモータは周りの部品に大きな影響を及ぼすため,十分な衝撃対策を施す必要がありました。」(B氏)
このように技術的なハードルが予想されるなか,B氏らは改善策を求め情報収集を続けました。
B氏は,過去に他の案件で実績のあった山洋電気にこうした課題を相談しました。相談を受けた山洋電気の担当者は,B氏にサーボモータ「SANMOTION R」(フランジサイズ20mm角)を提案します。
「サーボモータならば締めたネジ1本ごとのトルク値を出力できるので,外部装置にデータを保存することで,製造時のエラーに対して問題の部材を速やかに特定できるようになります。トレーサビリティの徹底とともに,これを応用すれば今後,故障予知やIoTによるスマートファクトリー化への展開も見込めます。
また,提案していただいたフランジサイズ20mm角のモータは,装置の小型・軽量化に大きく貢献すると思われました。」(B氏)
しかし,モータのスペックを見たB氏は難色を示します。標準仕様の最高回転数(rpm)ではA社が求めるサイクルタイム短縮は実現できなかったのです。
「このモータは小型でも高いトルクが特長でしたが,最高回転数は当社が求めるスペックに達していませんでした。こうした点を指摘すると,担当者はさらに使用条件を精査し,回転数の引き上げは十分可能と追加提案してくれました。」(B氏)
山洋電気はB氏らと技術ミーティングを重ねながら耐久試験や検証を続け,モータの最高回転数を引き上げるカスタマイズをおこないました。さらに動作パターンの見直しでモータに掛かる負荷を抑えて目標値を達成しました。
「山洋電気にはカタログスペックにこだわることなく,当社の使用条件に寄り添った技術協力をおこなっていただきました。こうしたカスタム提案は他社にないもので,おかげで期待を超える性能を達成できました。これからもいろいろと相談に乗ってもらいたいと思っています。」(B氏)
公開日: