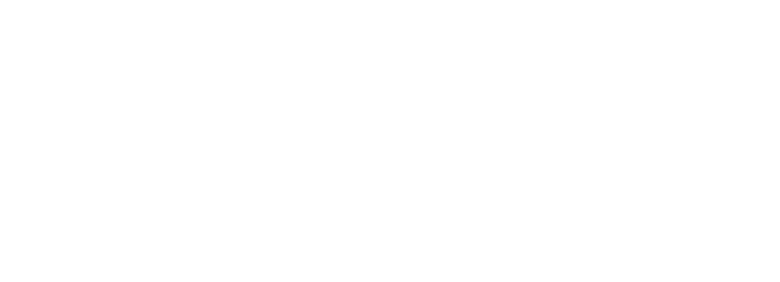
工場設備の突然の故障,防げていますか?工場の機械などの設備が突然故障することの影響は,修理費が発生するだけではありません。修理期間中に生産ラインがストップしてしまうことで,生産が遅延し,ラインのダウンタイム中に得られたはずの利益の損失にも繋がってしまいます。
では,突然の故障を防ぐにはどうすればよいのでしょう。そのためには保全(メンテナンス)が欠かせません。今回は,保全にはどのような種類や方法があるのか,最近「予知保全(予兆保全)」がさまざまな企業で重視されている理由,工場においてはモーターの故障の予兆を検知する「予知保全」が重要な理由などを解説します。
予知保全とは,工場の機械などの設備を常に監視して部品の劣化状態などを把握し,「そろそろ故障しそうだ」という予兆を検知したタイミングで,機械や設備が故障する前に部品の交換や修理などの保全(メンテナンス)業務をおこなうことです。
予防保全では,例えば「この機械は5年ごとにメンテナンスが必要です」などと,あらかじめ機械メーカーから提示されている情報をもとに,計画的に保全業務をおこないます。
故障する前に保全業務をするという点では先述した予知保全(予兆保全)と一緒ですが,もとからの計画的な保全業務かどうかが異なるポイントです。
事後保全は,事後という言葉通り,故障してから保全業務をすることです。生産ラインがストップしてしまう期間を極力短くするため,いかに迅速に故障原因の確定と修理作業をおこなうかが求められます。
しかし,事前の保全であれば部品の交換だけで済んだはずのことが,事後保全だと作業範囲も増え,作業費も膨らみがちです。また,部品の在庫がない場合は,部品が届くまでラインがストップしてしまうなど,費用がかかり,利益の損失も大きいものになってしまいます。
工場の機械などの設備が突然故障することの影響は,修理費が発生するだけではありません。一般的に生産現場では,生産計画に基づいた高い稼働率での生産が求められます。
しかし,故障による修理によって生産ラインがストップしてしまうことで,ダウンタイムが発生し,生産遅延やダウンタイム中に得られたはずの利益の損失にも繋がってしまいます。そのため,いかに故障を防ぐかが,現場では長く課題とされてきました。
事後保全は,先述した通り「壊れたら修理する」という考え方で,そもそも防ぐことを目的としていません。
計画を立てて定期的にメンテナンスをする「予防保全」は昔からおこなわれてきた方法であり,計画通りの保全を徹底することで,ある程度故障の可能性を減らすことはできます。
しかし,定期的な交換後に,たまたま何かの部品の調子が悪くなってしまうことは,起こりえることです。予防保全ではそのようなケースを完全に防ぐことはできません。
また,予防保全では,故障の可能性を少しでも減らそうと,ついメンテナンスの頻度を増やしがちです。
メンテナンスの頻度を上げると,まだ本来なら使えるのに部品を交換することになり,交換部品代がかさみ,作業費もかかってしまいます。
予知保全(予兆保全)では,工場の機械などの設備を常に監視して,部品に一定の度合いの劣化や変化が起こった際に,故障の予兆とみなして保全作業をおこないます。
そのため,予防保全のように定期交換だからと,まだ使える部品をすべて交換したりする必要がありません。交換が必要なタイミングで,最小限の部品代・交換作業費で済ませることができるので,コスト削減の効果も見込めます。
予防保全で定期的な交換をおこなっても,何らかのタイミングで次の交換タイミング前に劣化や不具合が出ることはあります。
予知保全(予兆保全)であれば,振動などの波形を常に監視することで異常を検知でき,保全作業ができるため,故障を予防できる可能性が高くなります。
IoT/AIなどの監視システムの構築に伴い,構築コストが必要になる点がデメリットです。
これについては,故障というリスクに対して,壊れたら修理すればよいものに対しては事後保全,極力防ぐ必要のあるリスクについては予知保全をおこなうなどの整理をして,適切なコストを算出し費用対効果を試算する必要があります。
一般的に予知保全をおこなうためには,まず,監視する対象の装置に対して,振動や温度など必要な情報を収集するためのIoTセンサを取り付ける必要があります。
また,そのセンサからデータを集めて,分析するシステムも必要となります。その後,それぞれのデータのなかで,どの数値を異常の予兆とみなすかといった仮説と検証を繰り返しながら,最適な値を見つけていく作業が必要になります。
高精度な位置決めや回転制御に不可欠なサーボモータは,さまざまな業種における工場設備に使われています。そのため,サーボモータの予知保全をきちんとおこなうことは,工場の安定稼働のためにも非常に大切です。
サーボモータの故障を防ぎたいということであれば,予知保全機能の付いたサーボモータ・アンプを使うことも選択肢のひとつです。
予知保全機能の付いたモータ・アンプなら,保持ブレーキの残寿命の予測や,制御電源の過電圧ワーニングと周波数モニタ,主回路電源品質モニタ,上位通信品質モニタ(EtherCAT),エンコーダ通信品質モニタなどの機能を搭載しており,サーボシステムや装置の故障の原因となる要素を特定できます。
また,部品寿命の通知により,機械装置のダウンタイムをなくすことができます。
ここで,山洋電気製ACサーボシステムACサーボシステム「SANMOTION G」の特長をご紹介いたします。
電源状態と通信品質の監視や,保持ブレーキ寿命の予測,電子部品の故障予防など,安心・安全にご使用いただくための機能を充実しました。また,バッテリレスエンコーダなので,バッテリ交換が不要です。機械装置の信頼性とメンテナンス性が向上します。
装置を高速かつ高精度に力強く制御でき,装置の生産性と加工品質の向上に貢献します。当社従来品※1と比べて,以下のサーボ性能の向上を図りました。
※1:当社従来品サーボシステム「SANMOTION R」との比較。
※2:サーボアンプからの速度指令にモータがどのくらい安定して追従できるかを示した周波数。
耐振動性能は,サーボモータは当社従来比※3で2倍,サーボアンプは20%向上しました。サーボアンプの使用温度範囲は約10%拡大し,0~+60℃です。標高2,000mの高地でも使用できます。耐環境性能が向上したので,さまざまな地域と環境でご使用いただけます。
※3:当社従来品サーボシステム「SANMOTION R」との比較。
さて,ここまで予知保全(予兆保全)についての概要と予知保全を実現する方法をご紹介してきました。
予知保全はすでに製造・エネルギー・医療などさまざまな業界で一般的になってきており,今後さらにさまざまな分野への展開が予想されます。
食品や化学品などの原材料を攪拌する,攪拌機などの装置を製造・販売するT社。
同社の納入先の一つである食品メーカーでは,装置の故障によるダウンタイムが与えるダメージに悩まされていました。
装置が停止すると,生産途中の製品が廃棄になり,原因が特定できるまでラインを再稼働できないことから,生産性や収益性に対する影響は甚大です。食品メーカーは新たな保全計画を企画し,T社にも予知保全をおこなうことができる撹拌機の開発を依頼してきました。しかし,コスト面での要求が厳しく…。
困ったT社は付き合いのある山洋電気の営業担当に相談しました。
山洋電気は,課題をヒアリングしたうえで、この攪拌機では重大な故障はモータに起因するケースが多いと分析し,ACサーボシステム「SANMOTION G」を提案。
重大な故障を引き起こす可能性のある要素を事前に察知できるようになったことで,予知保全の精度が高まり,ダウンタイムのリスクが軽減できるようになりました。これは計画的に生産を進めるうえで重要な要素になります。
監修:山洋電気株式会社 営業本部 サーボシステムビジネスグループ
更新日:/公開日: