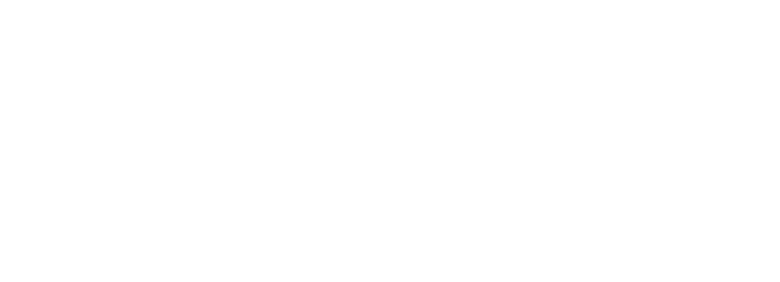
「용접·접합」은, 모든 산업에 활용되는 필수 불가결한 기반 기술입니다. 최근, 많은 메이커가 생산 라인 효율화를 위해서, 용접·접합 공정의 자동화를 진행해 왔습니다만, 이 공정은 무엇보다도 “품질 확보”가 요구되고 있습니다. 또한 용접 품질 향상을 위해서는 칩 드레서 등의 주변 기계가 필요하지만, 용접시의 작업 공간 확보를 위해 주변 기계의 소형화도 동시에 요구되고 있습니다.
용접 로봇 및 주변 기계에는 높은 신뢰성이 필요하지만, 용접기는 노이즈의 발생원이기도 하고, 주변 기계의 오작동이나 고장을 일으키기 쉽다는 약점을 가지고 있습니다. QA(품질 보증)나 안전성의 관점에서 많은 개선해야 할 과제를 안고 있습니다.
C사는 금속접합의 기술력을 축으로 산업기계 및 FA시스템 관련 제품의 제조·판매를 다루고 있습니다. 특히 아크/스폿 용접 로봇과 주변기기 분야에서 국내외 점유율 확대를 노리고 있습니다.
이 회사는 용접 로봇 주변에 설치된 '칩 드레서'에서 사용자가 받은 몇 가지 과제를 안고 있었습니다.
그 하나가 "소형화". 칩 드레서는, 용접 건 선단의 전극부를 연마해 용접 정밀도를 일정하게 유지하는 장치로, 용접 로봇에는 반드시 장비되고 있습니다. 최근, 제품 개발의 고도화·고속화와 함께 생산 라인이 과밀화하는 가운데, 생산 효율성의 관점에서, 칩 드레서에도 공간 절약화가 강하게 요구되고 있습니다.
그 점, 동사의 현행 모델에 채용되고 있던 DD(다이렉트 드라이브) 모터 시스템에서는, 고효율, 저소음이라고 하는 큰 메리트를 가지는 한편, 쿨런트액 침입에 의한 모터 고장이라는 문제를 안고 있었습니다. 또한, 현행 DD 모터는 모터 직경이 크고, 모터와 용접 로봇 제어부와의 센서 I/F(인터페이스)가 달라, 「센서 신호 변환 박스」가 필요했기 때문에, 장치 전체의 대형화, 또한 코스트 가 높아진다는 마이너스면을 불식하지 못하고 있었던 것입니다.
그리고 두 번째 큰 과제는 TIG 노이즈로 인한 장치의 오작동으로 시스템이 멈추고 생산 라인의 가동률이 저하되는 것이었습니다.
용접 시스템은 그 원리상 대전류가 발생하기 때문에 극단적으로 말하면 "노이즈의 원흉"이라고도 할 수 있습니다. 스폿 용접시에는, 이 대전류와 함께 컷하기 어려운 TIG 노이즈가 발생해, 이 노이즈를 엔코더나 콘트롤러, 센서 신호 변환 박스가 주워 버리는 것으로, 본래의 파형 출력에 광미가 생겨, 오작동 및 고장을 일으킨다 원인이 되었던 것입니다. 회사 기술 개발부 부장의 A씨는 이렇게 말합니다.
"불량이 빈발함에 따라 공장 생산 라인에 가동률 저하를 초래하고 있다는 보고를 받아 당사의 기술자가 검증한 결과, 기존 모터 시스템의 신뢰성에 어려움이 있음을 알게 되었습니다. 칩 드레서는 높은 정밀도의 연마 능력과 높은 신뢰성이 요구되기 때문에, 중대한 개선 요구로서 한번도 빨리 해결시킬 필요가 있었습니다.
※TIG(티그) 노이즈: TIG 용접시에 발생하는 노이즈. TIG 용접이란, 비용극식의 이너트 가스 용접으로, 텅스텐 또는 텅스텐 합금을 전극으로 하는 용접. 용접 재료에 용가봉을 사용하여 전극이 용접 재료가 되지 않는 비용극식(비소모 전극식)의 가스 실드 아크 용접. TIG는 Tungsten Inert Gas의 약자.
현행기의 문제 해결을 위해 정보 수집을 하고 있던 A씨는, 거래처로부터의 소개로 산요전기의 영업 담당과 이야기할 기회를 가집니다. 자사의 칩 드레서가 안고 있는 문제에 대해 상담한 A씨는, 후일, 현행의 φ180mmDD모터에 의한 구성을 「80mm각 AC서보모터+기어」구성으로 변경하는 제안을 받습니다. 이것은 A씨에게 있어서 바로 「눈으로부터 비늘의 제안이었다」라고 합니다.
「목표로 하고 있던 것은, 100mm 이내의 사이즈였지만, 제안해 주신 AC 서보 모터+기어는, 80mm각으로 DD 모터에 비해도 매우 소형이었습니다.또, 로봇 컨트롤러와 같다 I/F의 센서를 탑재했기 때문에, 「변환 박스」를 없앨 수 있었습니다. 그 결과, 장치 구성이 간략해지고, 더욱 소형화할 수 있을 것으로 기대가 있었습니다. 게다가 모터 본체에 있어서 IP67의 보호 등급에 대응하고 있어 쿨런트액 대책도 향상한다… "(전출 A씨)
「센서 신호 변환 박스」를 없앤 것은 두 번째 과제였던 「노이즈 대책」에도 유효했습니다. 변환 박스가 TIG 노이즈를 주워 버리는 것으로, 센서 파형이 미치고, 올바른 신호를 읽을 수 없는 요인이 되었으므로, 원래의 문제 발생의 원인이 없어지는 것입니다.
“현행 모델에서는 모터 경량화를 위해 수지제 커버를 사용하고 있었습니다만, 노이즈 내량이 높은 철제 커버의 채용을 제안해 주었습니다.수지제와 철제 커버의 내노이즈 평가의 결과도 제시해, 향상하고 있는 것을 잘 알았습니다.또, 노이즈 대책에 최적인 배선이나 노이즈 필터의 설치 등, 노하우를 여러가지 제안해 주셨습니다.
얼마 지나지 않아 회사와 산요전기는 프로토 타입을 제작하고 평가 테스트를 실시했습니다. 약 6개월에 걸친 평가 시험의 결과, 지금까지의 제안 내용이 이론치가 아니고, 현실치인 것을 확인하기에 이릅니다.
이러한 검증을 거쳐, C사는 산요전기「고성능 AC 서보 모터+기어」를 채용한 칩 드레서의 신모델 양산화를 결정했습니다. A씨는 이렇게 총괄합니다.
「산요전기의 제안은, 유저로부터의 요구를 채우고, 장치 성능을 향상시키기 위해서 빠뜨릴 수 없는 것이었습니다. 프로토타입에 의한 평가 기간은 반년에 걸쳐 계속되었습니다만, 그동안도 산요전기 에는 모터 메이커의 틀을 넘어, 유연한 기술 서포트를 행해 주셔서 매우 고맙게 느끼고 있습니다.」
게시일: