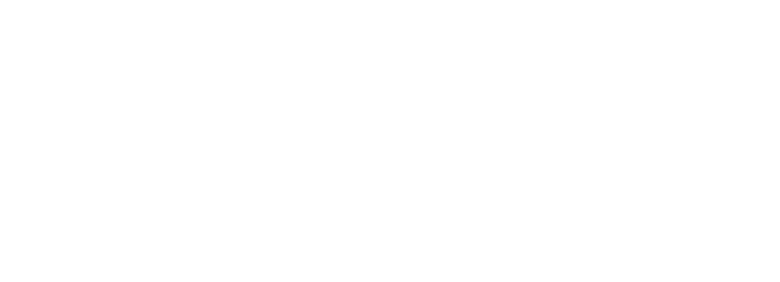
Company N is a medical equipment manufacturer that supplies major medical equipment manufacturers with OEM products such as hemodialysis, peritoneal dialysis, infusion-related products, and blood purification devices. In recent years, as the need for dialysis treatment has increased both domestically and overseas, securing a stable share in the market, which is expected to expand, has become a major issue.
Since dialysis equipment is directly linked to maintaining the lives of patients, reliability is of utmost importance, and equipment must operate stably and with long-term durability that reduces the risk of accidents. Equipment failures and malfunctions not only threaten the health of patients, but also place a burden on patients and lead to losses for hospitals due to the waiting time until equipment is restored.
Additionally, N Company had a variety of requests, such as reducing noise and vibration of the equipment to alleviate stress on patients who would be using it for long periods of time, mainly in a hospital environment.
To continue to meet these market needs, it is necessary to constantly release products with the latest specifications for each model, which in turn requires parts to be customized to fit the size and shape of the equipment.
However, machining parts to fit the size and shape of the device requires a huge number of man-hours, and parts manufacturers are reluctant to meet detailed orders. This situation is one of the reasons that development times are long.
"When developing a product, several stages of prototyping and evaluation are carried out between the manufacturer and the product. Since the delivery date for the prototype is fixed, from the designer's point of view, the truth is that we want to spend as little time as possible selecting parts. This is because, even if there is a need to go back and remake the prototype, we want to ensure there is enough time to do so."
Mr. K of the Design and Development Department at Company N said, "In a competitive environment, we needed to shorten the development lead time more than anything else in order to stand out from the competition.
One day, when Mr. K consulted with a SANYO DENKI sales representative about developing a new dialysis machine, the sales representative suggested a three-phase stepping motor as a product that could significantly reduce vibration and also had cost benefits.
"Dialysis equipment needs to operate smoothly at an extremely slow speed in accordance with the human internal circulation. Vibrations and uneven speeds affect patients as pressure changes, so we want to minimize them as much as possible. However, the ideal low-vibration drive cannot be achieved with a two-phase stepping motor, and it is also difficult to achieve with a five-phase stepping motor due to the cost. However, when we proposed using a three-phase stepping motor for micro drive, we felt that we had found a clue to solving these conflicting issues." (Mr. K)
Generally, two-phase stepping motors are inexpensive but have rough operation, while five-phase stepping motors have fine operation but are expensive. In this regard, SANYO DENKI 's three-phase Stepping Systems" SANMOTION F3 ( 3-phase )" is said to achieve the same low noise and vibration as a five-phase stepping motor while offering cost benefits by using the company's driver function "microstep drive"(*).
(*)Microstep drive (Vernier drive): A technique for obtaining finer step angles by finely varying the current ratio rather than simply turning the current to the windings on and off.
Furthermore, manufacturers that manufacture and sell three-phase stepping motors are rare in Japan, and SANYO DENKI was one of the few companies that could do so, which further supported Mr. K's decision. Thus, Company N decided to evaluate and introduce the "SANMOTION F3 ( 3-phase )" as a solution to improve the basic performance of their equipment.
When the motor was actually operated alone, the noise and vibration levels were as expected. Company N immediately adopted SANMOTION F3 ( 3-phase ) for a new dialysis machine. However, an evaluation of the first prototype indicated that it did not meet the noise target.
The cause was that the resonance points overlapped with other parts when it was installed in the device. N Company immediately started to manufacture a new prototype, but what satisfied Mr. K was the speedy follow-up system of SANYO DENKI.
"They were able to handle the custom machining of the shaft shape, and even when we had to rework things during the evaluation stage, they quickly reordered the prototype motor within two to three days. This was something that other companies didn't offer. Thanks to that, we were able to have enough time to evaluate the product." (Mr. K)
SANYO DENKI was able to provide Company N with an evaluation motor in a timely manner thanks to its experience and track record of customizing products for a variety of companies. After this, the company continued to respond quickly to each trial and error that occurred during prototype production, helping to shorten Company N's development time.
After these prototypes and evaluations, Company N began mass production of the new dialysis machine in 2008. In the two years from 2008 to 2009, the company achieved a record of zero quality or delivery issues. Company N's dialysis machine, which has been highly praised by users, is also being used overseas, and the order amount has increased in 2010. Mr. K sums up the adoption this time as follows:
"SANYO DENKI 's support system, which could be described as a team effort, from proposing the optimal motor to quickly delivering parts, has made a major contribution to improving our reliability."
Company N's reliability will continue to ensure it a strong competitive edge in both domestic and international markets.
For more information about stepping motors, please see "What is a stepping motor? An explanation of its structure, types, usage (drive system and control method), advantages and features."
release date: