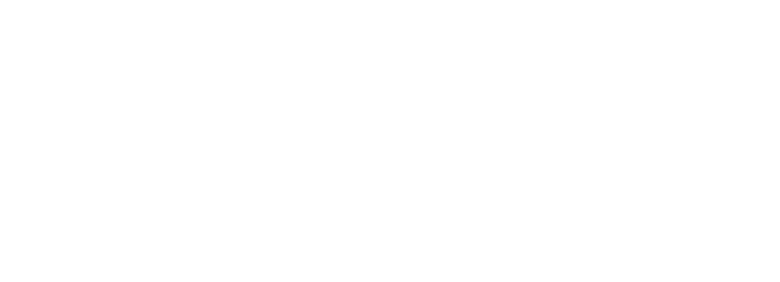
A stepping motor is a type of controlled motor that moves and rotates at a fixed angle like a clock by switching the phase through which current flows. It can be positioned without a sensor. It is also called a pulse motor, step, or stepper motor.
Depending on their structure, stepping motors are classified as 2-phase, 3-phase, and 5-phase.
For a stepping motor that rotates like a clock, the angle that can be moved with one pulse is called the "reference step angle." The finer the reference step angle, the smoother and more precise the movement will be.
A driver is required to drive a stepping motor. When making a driver, please be aware that in the case of a two-phase motor, the driver circuit differs depending on whether it is a bipolar or unipolar drive. For three-phase and five-phase motors, a driver that can pass current in both directions is required.
In addition, because two-phase and three-phase stepping motors have a simple winding structure, the same drive circuit can be used to rotate the motor, even if the manufacturer is different. However, five-phase stepping motors have a complex winding structure, and there is not just one combination or order of phases that must be combined to rotate the motor. Therefore, when using a five-phase stepping motor, care must be taken when choosing a driver.
First, regarding the pulse command signal, this is an electrical signal in which the voltage is repeatedly turned ON/OFF (HI/LOW). One cycle of HI/LOW is counted as one pulse.
Pulse signals are input to the driver from a host controller, etc., and the rotation angle is controlled by the number of these pulse signals.
Stepping motor speed control
The rotation speed is controlled by the density of the pulse number. If one pulse rotates one reference step angle, sending 10 pulses per second will rotate a larger angle per second than sending one pulse per second. Therefore, the higher the pulse frequency, the faster the rotation speed.
Stepping motor position control
Recent drivers use a microstep method that enables positioning at angles smaller than the motor's reference step angle by precisely controlling the amount of current flowing through each phase, enabling even more precise position control.
Advantage 1: Easy to control
It can be easily rotated by simply turning the driver transistor on and off correctly. The rotation speed can also be easily increased by simply accelerating the ON/OFF timing.
Advantage 2: System simplification possible
Since the motor can be easily controlled by the pulses and their frequency input to the driver, no complex controller is required. In addition, the greatest feature of stepping motors is that they can control position and speed without a detector, which makes it possible to simplify the system.
Advantage 3: Low-cost system construction possible
The system can be built inexpensively because the driver is simple, no detector is required, and no complex controller is required.
Advantage 4: Stable stopping is possible
Since a stepping motor is a motor that is stopped by magnetic force, it generates a stopping force (holding torque) which allows it to come to a stable stop.
Although we do not see stepping motors directly in our daily lives, they are at work inside many machines that support our lives in a variety of situations. Where are they actually used? The following are some typical examples of their applications.
For more information, please see "What is a stepping motor? Applications and usage examples of stepping motors."
Caution 1: Loss of synchronization
No sensor is required, but since the position is not confirmed, it is not possible to notice if the motor is not moving according to the command (losing synchronism). It is less reliable than a servo motor with closed loop control.
Caution 2: High fever
Since a holding torque is generated even when the engine is stopped, heat is generated.
Note 3: Vibration
A motor rotates at a fixed angle at a time, moving one step at a time like going up or down a staircase, and so inevitably vibrates when moving.
Stepping motor | Servomotor | |||
control | Open Loop | Closed Loop | ||
torque | Without detector | A constant torque is always generated in the direction that stops the motor. | Motor Current Detector | The motor current is controlled in the direction that rotates the motor to generate the commanded torque. |
Rotational speed | Without detector | It rotates at a speed synchronized with the input pulse frequency. If it cannot synchronize, it will step out. | Motor Speed Detector | The motor speed is checked while moving so that the motor rotates at the commanded speed. |
Position (angle) | Without detector | It moves by the number of input pulses. If the movement is not completed in time, it will step out. | Motor Position Detector | The motor position is checked while moving so as to reach the commanded target position. |
Features | Cheap and easy to use, high torque at low speed | Expensive but has various functions and high torque up to high speeds | ||
friction | Even with high friction, positioning is possible quickly and accurately. | Precise positioning is possible, but it takes time if friction is high. | ||
Resonance and vibration | The speed ripple is large and the resonance cannot be suppressed by the motor. | Speed ripple and resonance can be suppressed using the driver's functions. | ||
Inertia Ratio | If the inertia is too large, the motor cannot be controlled. | The motor can be controlled even if the inertia ratio is large. | ||
Special skill Different uses |
Keep the same position. | Rotate stably (without vibration or noise). | ||
Low speed, short distance start/stop operation. | High speed, high acceleration start/stop operation. | |||
Light machining operation. | Precision machining, heavy-duty operation. |
release date: