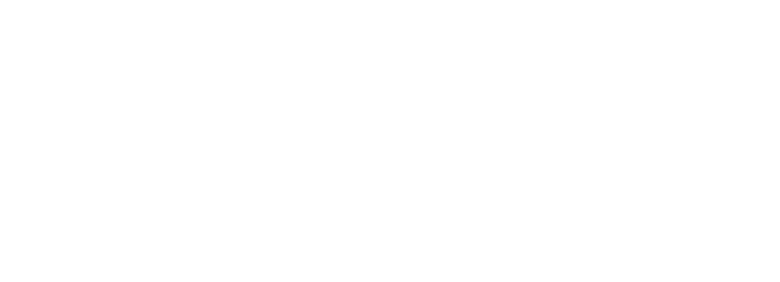
Motors are devices that generate mechanical power from electrical power. They are used in all kinds of moving things, from familiar home appliances such as washing machines, electric fans, and air conditioners to social infrastructure such as ATMs (automated teller machines) and automatic ticket gates.
In that sense, it can be said that everyone living today enjoys the benefits of motors in their daily lives. In addition to motors, there are other power sources that generate mechanical power, such as engines and steam engines.
However, motors have three features that other power sources do not have.
For example, the thermal efficiency of a typical engine is said to be 30 to 40%, which means that only 30 to 40% of the energy input is converted into power, with the remaining 60 to 70% being wasted as heat.
On the other hand, the energy conversion efficiency of a motor is over 80%. Thus, compared to an engine, energy can be converted into power without waste.
An engine is made up of many mechanical parts, each of which must be manufactured with high precision. In addition, many sensors are used to electronically control the engine, making the control complex.
Compared to engines, motors have a simpler structure and can be powered directly by electricity, making them suitable for precise electrical control.
It is important to remember that an engine burns gasoline to convert it into power, which inevitably results in the emission of carbon dioxide (CO2). In contrast, a motor does not emit any gases by itself.
As the movement towards achieving carbon neutrality accelerates, great expectations are being placed on motors.
Due to these characteristics, motors are currently used as power sources and control devices for a wide variety of equipment and devices, and their use is expected to increase in the future.
Related article: Knowledge "What is a stepping motor? Explanation of its mechanism, types, usage (drive system and control method), advantages and features"
Here we explain in more detail how stepping motors work and what their features are.
Motors were invented and have evolved in line with the flow of technological innovation in society.
Originally, humans moved things using human or animal power. Moving things with one's own power has been commonplace in the past and continues to be so today. It is said that horse-drawn carriages were invented before Christ, and as we all know, Japanese aristocrats in the Heian period used oxcarts.
However, no matter how much human or animal power was used, there were limits to the speed and strength that could be exerted.
The Industrial Revolution, which took place from the late 1700s to the 1800s, brought about major changes in this type of power.
The steam engine, with power far greater than that of humans or animals, appeared, and factory-based mechanical industry was established. Social structure changed from an agricultural society to an industrial one. Furthermore, the development of steam locomotives, steam automobiles, and steam ships greatly changed the nature of transportation and logistics. However, steam engines had the disadvantage of being large and heavy.
Inventors and researchers began searching for an alternative power source to the steam engine, and the motor emerged during this revolution.
British scientist Michael Faraday discovered the principles of motors and generators in 1821. He discovered the law of electromagnetic induction in 1831, which would go on to be applied to motors.
After Faraday, the DC motor (direct current motor) was developed by Thomas Davenport and others in the United States, but it took a while to become practical.
The first practical motor was probably the two-phase AC induction motor invented by Nikola Tesla. In 1888, Tesla developed a polyphase induction generator to rotate the motor he invented, and obtained a patent for it in 1889. This marked the beginning of practical use of motors.
Since then, motors have continued to evolve, taking on roles not only as a power source but also as a control device. It is said that 50% of electricity in Japan is currently consumed by motors. That is how deeply motors are involved in human life and support civilization.
The history of SANYO DENKI 's motors dates back to the first half of the 20th century.
First, in 1932, they developed a generator with the same basic structure as a motor for use in wireless communication equipment. In 1952, they shifted the rotating machines they had been manufacturing for military communication power supplies to civilian use, and SANYO DENKI went on to become a major manufacturer in the fields of telecommunications and power supplies.
In 1952, Sanyo Denki received a request from the Electrical Testing Laboratory (now the National Institute of Advanced Industrial Science and Technology) to develop a servo motor, and began research. Soon after, they completed Japan's first servo motor. At first, there was not as much demand as expected, and it took a while to see the light of day, but this became the foundation of the current SANYO DENKI, whose main product is servo motors.
After completing the servo motor, we also completed Japan's first stepping motor and the first fan. While developing these "Japan's first" products, we rode the wave of OA (office automation) and FA (factory automation) and expanded our range of motors globally.
Motors basically rotate by utilizing the "property that opposite poles attract each other" and "property that like poles repel each other" of magnets.
For example, imagine a small motor used in radio-controlled cars, etc. Inside the small motor is a coil with a rotating shaft and permanent magnets with north and south poles arranged on either side of it.
When electricity is passed through a motor, the coil becomes an electromagnet. It is easier to understand if you think of the coil as changing into a magnet with a north pole and a south pole.
Then, the N pole of the permanent magnet and the N pole of the coil will repel each other, and the S pole of the permanent magnet and the S pole of the coil will repel each other. At the same time, this also means that the N pole of the permanent magnet and the S pole of the coil will attract each other, and the S pole of the permanent magnet and the N pole of the coil will attract each other.
This causes the coil to rotate 180 degrees around its axis of rotation.
However, this alone will cause the coil to stop after rotating 180 degrees. This is because the N pole of the permanent magnet and the S pole of the coil attract each other, and the S pole of the permanent magnet and the N pole of the coil remain in this state of attraction. How can we rotate it another 180 degrees to make a 360-degree rotation of the axis of rotation?
By changing the direction of the electricity flowing through the coil, the positions of the north and south poles are swapped.
In the stationary state mentioned earlier, the N pole of the permanent magnet was attracted to the S pole of the coil, and the S pole of the permanent magnet was attracted to the N pole of the coil. Then, the direction of the electricity passing through the brushes is changed by a part called a "commutator," switching the N and S poles of the coil.
Then, the north pole of the permanent magnet and the north pole of the coil repel each other, and the south pole of the permanent magnet and the south pole of the coil repel each other. At the same time, the north pole of the permanent magnet and the south pole of the coil attract each other, and the south pole of the permanent magnet and the north pole of the coil attract each other. This causes the coil to rotate another 180 degrees. It has now rotated 360 degrees.
The motor rotates continuously by repeating this series of movements.
From here, we will introduce "motors as power sources" and "motors as control devices."
Motors that power facilities and equipment are mainly divided into two types, "DC motors" and "AC motors", depending on the power supply.
A "DC motor" is a motor that runs on direct current electricity.
They are used in a wide variety of things, from electrical appliances we use every day to equipment used in factories.
There are two types of DC motors: "brushed DC motors" and "brushless DC motors." Brushes are components that transmit electricity to the coil.
A brushed DC motor has a coil on the inside and a permanent magnet on the outside, and rotates the rotor (rotating shaft) by passing direct current through the brushes. This is the motor with the simple mechanism introduced first, and is used in radio-controlled cars and models.
The main feature of this motor is that the rotation speed increases in proportion to the voltage.
For example, when a brushed DC motor is powered by dry cell batteries, it will rotate faster when two batteries are connected than when one is connected. However, because the commutator that changes the direction of electricity flowing through the coil and the carbon brushes are in constant contact with each other, they will wear out after long periods of operation, and so regular maintenance is required.
On the other hand, brushless DC motors (BLDC motors) have a permanent magnet on the inside and a coil on the outside, and the inner permanent magnet is rotated by passing electricity through the coil via a current control circuit.
The absence of brushes not only reduces the frequency of maintenance, but also allows for use in clean environments because no brush wear debris is produced. However, a circuit is required outside the motor to control the direction of the current, which makes it more expensive than a brushed DC motor.
Motor Type |
merit | Demerit |
---|---|---|
Brushed DC Motor | low cost | Deterioration is rapid |
Brushless DC Motor | Long life | High cost |
An "AC motor" is a motor that runs on alternating current. It has a coil on the outside and a "squirrel-cage" rotor on the inside.
The advantage of AC motors is that they do not require commutators, brushes, or control circuits. Because of their simple structure and low manufacturing costs, they are used in a wide range of applications, including home appliances such as electric fans and vacuum cleaners, water pumps, transport conveyors, and industrial equipment.
Typical examples of motors used to precisely control the operation of devices and equipment are "stepping motors" and "servo motors."
A stepping motor is a motor in which the rotor rotates a fixed angle (position).
Imagine an analog clock. The second hand moves one second at a time. Stepping motors can be controlled to move only a set angle like this. In addition to analog clocks, stepping motors are used in printers, air conditioner louvers, ATMs, ticket vending machines, automatic ticket gate systems, and more.
The mechanism for turning the rotor a precise angle is simple. The rotor of a stepper motor has many grooves in it. Electricity is passed through the motor, and when the rotor has moved the distance of the intended groove, the electricity is turned off. This causes the rotor to rotate a precise angle and then stop.
For example, a two-phase stepping motor generally has 200 grooves. One rotation of 360 degrees is divided into 200 parts, so the angle moved by each groove is 1.8 degrees. If you want to rotate the motor 18 degrees, you pass electricity through the motor and when the rotor has moved the distance of 10 grooves, the electricity is stopped.
To control a stepper motor, you need a controller. The role of a controller is to send a signal to the stepper motor that tells it how far to move. First, the act of turning the electricity on and off is counted as one pulse. When the controller sends a one-pulse signal to the stepper motor, the rotor rotates one groove and stops.
As in the previous example, let's say you want to rotate a two-phase stepping motor with 200 grooves by 18 degrees. In this case, send a 10-pulse signal from the controller. When the stepping motor receives the signal, it rotates 18 degrees, which is the equivalent of 10 grooves, and then stops.
Thus, a controller is required to control a stepping motor.
Like a stepping motor, a servo motor is a motor designed to rotate a rotor by a desired angle. However, there are clear differences between servo motors and stepping motors.
A servo motor rotor has no grooves, so there is no restriction to rotating the rotor in 1.8 degree increments. If a high-resolution sensor is used, the rotor can be stopped at a precise angle of one millionth of a degree.
Sensors are necessary for this control. In a servo motor, these sensors accurately detect the rotational position of the rotor, so it can stop at the intended angle. In addition, the sensors continue to monitor the rotor even after it has stopped, and if the stopping angle deviates, the system is automatically controlled to correct it immediately.
Above, we have introduced the role and types of motors, their history, operating principles, and structures.
Understanding the features of motors will lead to optimal motor selection and improved equipment performance.
SANYO DENKI handles a variety of motors. If you have any questions regarding motor selection, please contact us.
release date: