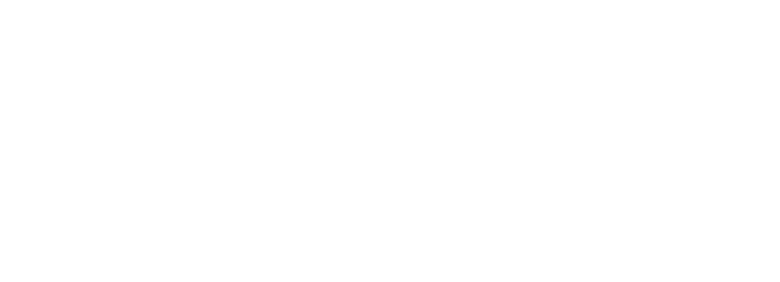
In response to the growing demand for digital devices such as smartphones and flat-screen TVs that are becoming smaller and more powerful, and for automobiles that are becoming more intelligent, many domestic semiconductor manufacturers are working hard to increase production. In addition, in the current semiconductor market, in addition to becoming smaller, thinner, and more multifunctional, prices are falling, and it is expected that analog devices will be rapidly replaced by other devices, such as mobile phones, which are becoming more popular worldwide.
In response to this trend, equipment manufacturers involved in each semiconductor manufacturing process are being asked to rapidly respond to technological innovations that correspond to miniaturization and high integration.
Company E is an equipment manufacturer that handles the "front-end" processes in semiconductor manufacturing.
In recent years, the development of advanced technologies has progressed at a rapid pace in the semiconductor industry, with mass production of devices with line widths of 32 nm (nanometers) already underway in some areas, and the development of device technologies for 22 nm and below also progressing steadily. Semiconductor technology is working closely with nanotechnology to accelerate the movement toward miniaturization and high integration.
Against this background, Company E is also required to develop equipment that can be developed in a short period of time to keep up with the rapid evolution of semiconductors, while also achieving high throughput and stable quality at low cost.
To achieve high throughput, it was necessary to review the performance of the transport section. Mr. S, the chief designer at Company E, explains the challenges in developing the new equipment:
"Our current machines use servo systems for areas that require speed and positioning precision, such as wafer transportation. When developing the new product, we considered increasing the size of the motor and developing new software to speed up the transportation section. However, this would take time to develop, and making the equipment larger would also result in a decrease in productivity per unit area."
The front-end process of forming circuits occupies a large part of the semiconductor manufacturing process, so a higher level of throughput is required. In addition, since the rate of production loss depends on the precision, stable quality must be achieved at the same time. Furthermore, due to the decline in the market price of semiconductors, it is necessary to consider reducing the cost of equipment in order to satisfy user demands.
While continuing to develop new equipment, Mr. S came across SANYO DENKI 's closed-loop Stepping Systems" SANMOTION Model No.PB ( Closed Loop )" at an industrial equipment event. After speaking with a sales representative, he learned that there was a case where a manufacturer had adopted this system and achieved dramatic improvements. Thinking that if it worked, they might be able to apply it to their own business, he asked for a detailed explanation.
In particular, what caught Mr. S's attention was that stepper motors have a larger torque at low speeds than servo motors, and that there is no "step-out" problem that is peculiar to stepping motors. Since the majority of E's equipment involves short stroke positioning, the high torque characteristics at low speeds worked to their advantage, and they expected to achieve improvements such as downsizing of the drive unit while maintaining the same positioning accuracy.
Company E immediately began evaluating "SANMOTION Model No.PB ( Closed Loop )". When they actually operated it, they found that there was no need for complex parameter settings like with servos, such as gain adjustments, and the system could be easily controlled by simply specifying the pre-set point numbers and program numbers with general-purpose I/O, so the evaluation process went smoothly. They obtained the following results.
Convinced of the improved performance of the transport section, Company E soon decided to adopt "SANMOTION Model No.PB ( Closed Loop )". By incorporating it into their new semiconductor manufacturing equipment, they achieved a significant improvement in performance. Mr. S sums up this adoption as follows:
"This time, we came across SANMOTION Model No.PB ( Closed Loop ), which led to a groundbreaking improvement in performance. By increasing speed while maintaining reliability, we were able to achieve the industry's highest level of throughput. The transfer section was reduced in size by roughly half, allowing for an increased number of additional units to be installed, dramatically improving productivity per unit area. Also, by replacing the previous servo system, the cost of the drive system was reduced by approximately 75%."
Company E's new equipment has been well received by users, and the company's equipment will likely continue to support semiconductor manufacturing in the future.
For more information about stepping motors, please see "What is a stepping motor? An explanation of its structure, types, usage (drive system and control method), advantages and features."
release date: