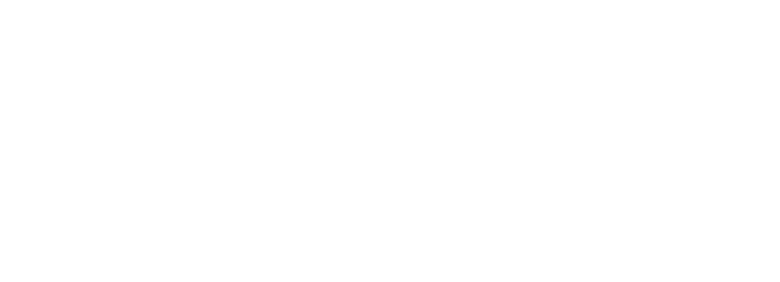
Although the semiconductor market has entered a mature phase, further growth is expected due to the spread of smartphones and tablet PCs. However, Japanese companies are still struggling. As market competition becomes more severe, the most pressing issues are not only securing technological superiority and building new business models, but also surviving in the midst of fierce cost competition.
In particular, the technical hurdles required for semiconductor manufacturing equipment have been raised to a new level, and conventional methods are no longer able to meet the demands for further efficiency improvements and cost reductions...
Company Y is an industrial equipment manufacturer that develops, manufactures, and sells a wide range of general industrial machinery as well as cutting-edge semiconductor manufacturing equipment and inspection equipment.
The company was facing a major challenge in developing a new model of semiconductor manufacturing equipment because the current model did not adequately meet the market needs for improved precision and cost reduction.
This device requires a suction mechanism, which requires air to pass through the ball spline, and the motor could not be placed on the same axis. For this reason, a timing belt was used, but there were issues with the timing belt. The tension of the belt mechanism can change significantly with even the slightest error, so it was difficult to maintain the appropriate tension. If the belt is too tight, the load increases and it can have a negative effect on the mechanism. However, if it is too loose, the belt will vibrate and, in the worst case, it may come off. Another weakness is that its accuracy is easily degraded due to aging caused by long-term operation.
So the company turned its attention to the advantages of hollow shaft motors instead of belt drives.
In a "hollow shaft motor," the motor shaft is hollow, so by attaching a ball spline to the hollow inner diameter, it is not necessary to use a timing belt or a large-scale transmission mechanism such as a gear. Also, by being freed from the weak points of belts, it is expected to be possible to significantly improve precision, simplify the mechanism, save space, and reduce costs. However, selecting a hollow shaft motor was not an easy task. Mr. H, a member of the company's development department design team, talks about the situation at the time as follows:
"The motor was a key element in terms of both performance and cost reduction, so we were very careful in our selection. However, even after gathering information from the Internet and catalogs, we found it difficult to find a product that met our requirements."
Later, a SANYO DENKI representative visited Company Y to confirm the specifications and heard detailed information about the required specifications from Mr. H and his team.
I took home the drawings of the current model and decided to first calculate the load inertia for each part and select a motor. As a result, I proposed a hollow shaft type motor (hollow diameter φ8mm) customized based on the "56mm square 2-phase stepping motor".
"The time from the first meeting to the proposal was only about one week, which was a very fast response. They also customized the motor so that we could continue to use the ball spline mechanism that we currently use." (Mr. H)
Next, Mr. H and his colleagues decided to carry out a prototype evaluation of various performance aspects of the proposed motor using an actual machine.
As a result of the verification, we were able to confirm various advantages of using a hollow shaft type stepping motor.
First, by passing a ball spline through the hollow inner diameter, we were able to greatly simplify the mechanism.
In addition, maintenance to maintain belt tension is no longer necessary, and problems caused by belt deterioration can be prevented.
Even if a breakdown did occur, the steps that were required with a belt drive - removing and replacing related parts to remove the belt, adjusting the belt tension, and reassembling the parts - were not necessary, but rather only replacement was required, shortening the equipment downtime and significantly reducing maintenance man-hours.
In addition, the positioning accuracy has been improved dramatically by directly transmitting the rotation of the motor.Furthermore, the hollow shaft allows linear and rotary motion with a single ball spline.
"In conventional equipment, separate ball splines were used for linear motion and rotation, but with this system, both functions can be mounted on a single spline, saving space and ultimately reducing equipment costs by 30%." (Mr. H)
After detailed verification, Company Y decided to officially adopt the "hollow shaft motor."
Mr. H had this to say about the implementation:
"By replacing the motor, we were able to improve the accuracy of the new model, reduce costs, and reduce maintenance work, just as we expected. SANYO DENKI provided us with a thorough understanding of our system, and provided us with a detailed response, from selecting the optimal motor to customization."
After the release of the new model, Company Y secured a significant market advantage as expected and steadily expanded its market share. It is making a significant contribution to reducing the cost and ensuring the quality of semiconductor products in the face of global competition.
For more information about stepping motors, please see "What is a stepping motor? An explanation of its structure, types, usage (drive system and control method), advantages and features."
release date: