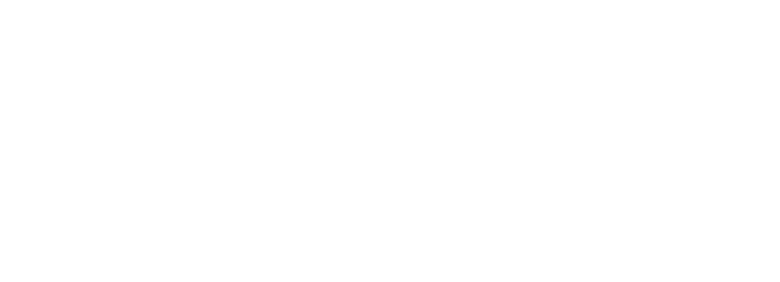
In recent years, industries in Asian countries have been rapidly shifting from traditional labor-intensive manufacturing to factory automation (FA), and many Japanese industrial mechatronics manufacturers are focusing on product development for Asian markets, including China and India.
However, market competition has intensified in recent years against the backdrop of the prolonged appreciation of the yen and the global economic slowdown. In order to secure market dominance and expand market share, in addition to "reducing production costs" with a view to price competition, "improving quality" has become an essential element.
Company S, which develops, manufactures, and sells various FA equipment, inspection equipment, and precision machinery, has decided to strengthen its global strategy in response to the sluggish domestic market in recent years. The company aimed to expand its share overseas for various inspection equipment, including its main product, "circuit board visual inspection equipment."
In particular, the company has been taking proactive measures to expand its product lineup and sales channels in Asian markets, including the growing markets of China, India, and Thailand. Due to the characteristics of these markets, the company has been developing lower-cost models of products for the domestic market and selling them to local manufacturers.
However, as market competition intensifies, simply pursuing a "low-price approach" would lead to a war of attrition and could become a factor in reducing profitability. In order to differentiate from competitors and successfully expand market share in the Asian market, the company needed to offer "high performance" at a low price. Mr. T, head of the company's Technology and Development Division, said:
"We expect that the automation of production processes will progress rapidly in Asian countries in the future, but simply lowering prices, as has been done in the past, will no longer be enough to compete with other manufacturers, including foreign-affiliated ones. In the future, in the Asian market, just as in Japan, 'reducing cycle time' by improving inspection efficiency will become an essential element."
Given this background, Mr. T decides to review the performance of the next model of the "PCB visual inspection equipment" for export.
In order to meet the market need for "reduced cycle time," it is necessary to improve inspection efficiency. First, we reviewed the transportation section, but the "mounted motor" in the current model was a bottleneck and we were unable to increase the transportation speed sufficiently.
"Due to cost issues, we used a stepping motor for the conveyor belt of the device. To increase the conveyor speed, we needed a 'higher torque characteristic,' but with conventional stepping motors, the torque drops significantly at high speeds, so we couldn't increase the speed any further," said Mr. T.
One solution would be to increase the motor size, but a larger motor would increase costs and also lead to an increase in the size of the equipment itself, reducing product competitiveness.
We needed to find a way to increase the speed without losing torque while keeping the current motor size.
"How can we increase the conveying speed while maintaining the necessary torque without changing the motor size?"
Searching for a solution, Mr. T decided to consult SANYO DENKI, with whom he had dealings through servo motors, about these problems.
SANYO DENKI 's sales representative listened to S Company's requirements in detail and made the following proposal:
"With stepping motors, there is a trade-off between increasing the torque and decreasing the maximum speed, and increasing the maximum speed and decreasing the torque. We can adjust the torque characteristics to meet your needs."
Shortly after, Company S received a prototype with customized winding specifications and installed it in an actual machine for testing.
"By finely adjusting the winding specifications, we were able to ensure the torque at the required speed and achieve optimal characteristics. I was amazed at their level of technical expertise. As a result, we were able to successfully increase the conveying speed by 10%." (Mr. T)
By not changing the motor size, we were able to avoid any cost increases and maintain the current equipment size.
Furthermore, it only took three weeks for Mr. T to receive the prototype, and he was also very satisfied with SANYO DENKI 's prompt response.
"Afterwards, we had the opportunity to tour the stepping motor production site (SANYO DENKI Kanagawa Factory). The manufacturing process and materials management were all systemized, and the production management system was completely visualized. This gave us the confidence to leave it to them even when mass production began." (Mr. T)
The proposal to change the flange and shaft length to match the conventional product was also a deciding factor, and Company S decided to officially adopt SANYO DENKI 's stepping motor.
Furthermore, by reviewing the inspection algorithm and other systems, the next model achieved a 25% reduction in cycle time, dramatically improving performance.
"SANYO DENKI did not just supply stepping motors, but also helped us to significantly improve the performance of our next model, something that we thought would be difficult to achieve, through flexible customization in line with our requirements. This will put an end to the price war, and we will be able to differentiate ourselves in the Asian market by leveraging the high quality and performance that only Japanese manufacturing can offer. We are also very grateful that they have always satisfied our needs, including the prompt delivery of parts."
For more information about stepping motors, please see "What is a stepping motor? An explanation of its structure, types, usage (drive system and control method), advantages and features."
release date: