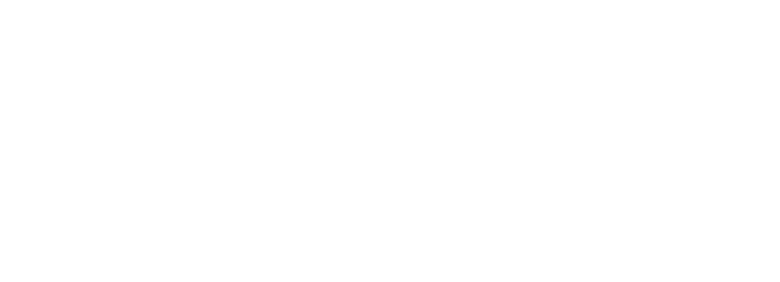
As electronic devices such as mobile phones and laptops become smaller and more powerful, the components on electronic circuit boards are becoming smaller and smaller, and the patterns are becoming finer. Even components less than 1mm in size can cause defects if they are not soldered accurately. For this reason, visual inspection of circuit boards is essential, and there is a demand for faster, more accurate inspection equipment.
Company B, which develops, manufactures, and sells a variety of FA systems and inspection equipment, has begun development of the next model of its PCB visual inspection equipment. PCB visual inspection equipment is essential for producing uniform, high-quality PCBs. The most important issue for the next model was to reduce the vibration of the transport part. Director A of the company's design and development department said the following:
"We were using a two-phase Stepping Systems for the transport section of our board visual inspection equipment, but we were having problems with vibrations when transporting the boards. A sensor was used to detect and position the moving board, but if the board vibrated as it moved, errors would occur in the sensor's detection and the stopping accuracy would decrease. We felt that the accuracy of the two-phase Stepping Systems was limited, but if we were to review the entire system, including the upper level, it would take too much time in development. We also had a limited development period, so we needed to find a solution quickly."
There was also the problem of increased noise due to vibration.
In addition, miniaturization of the device was also an issue to consider.
"We needed to downsize the equipment to be more competitive. We wanted to downsize the mechanism for the transport section, but making the motor smaller would result in insufficient torque, which could lead to a slower transport speed. Inspection equipment needs to be able to perform high-precision inspections at high speeds to help improve production efficiency. There's no point in sacrificing speed," said Mr. A.
Later, after hearing Mr. A's requirements in detail, the SANYO DENKI representative will make a proposal to him.
"A five-phase stepping motor can reduce vibration and noise. Our DC input microstep driver also has a two-phase mode to make it easy to replace a two-phase stepping motor. It also has an auto-micro function, so the driver always controls the motor in microsteps, regardless of the resolution setting. In other words, vibration and noise can always be kept to a minimum, regardless of the resolution setting."
Mr. A immediately obtained a sample and decided to verify the replacement of his two-phase Stepping Systems.
"When the five-phase stepping motor performed exactly the same way without changing the host system, I knew this was it. We expected that we could replace the system in a short period of time and also significantly reduce vibration and noise."
After detailed evaluation, it was confirmed that vibration could be reduced by 67% and noise by 30%. Furthermore, because vibration was suppressed, the stopping accuracy of the board and the positioning time were greatly improved, which led to a reduction in the cycle time of the equipment.
Furthermore, a SANYO DENKI representative suggested using a linear drive stepping motor for the push-up shaft that holds the board in place during inspection.
"We had been using a ball screw for the thrust axis, but they suggested we use a linear drive stepping motor instead. This suggestion made sense to me. The motor has a built-in ball screw, so we can eliminate the complicated structure. We were worried about the stroke, but it turned out that it was 80 mm, so that wasn't a problem. Until now, we had a structure of 'motor, pulley, belt, ball screw', but by consolidating it into a linear drive stepping motor, we were able to save space." (Mr. A)
Furthermore, since the stepping motor and ball screw are integrated, the mechanism has been simplified and the positioning accuracy of the thrust axis has been improved.
Having confirmed that the prototype performed as expected, Mr. A decided to replace Stepping Systems in the next model with SANYO DENKI 's 5-phase Stepping Systems" SANMOTION F5 ( 5-phase )" microstep model and linear drive stepping motor. Mr. A said:
"Thanks to flexible proposals based on our requests, we were able to obtain the optimal Stepping Systems. With the new model, we were able to reduce vibration as targeted, improve inspection accuracy, and reduce noise. We are very pleased that we were able to develop an inspection device that will help shorten the cycle time of our customer's production line."
For more information about stepping motors, please see "What is a stepping motor? An explanation of its structure, types, usage (drive system and control method), advantages and features."
release date: