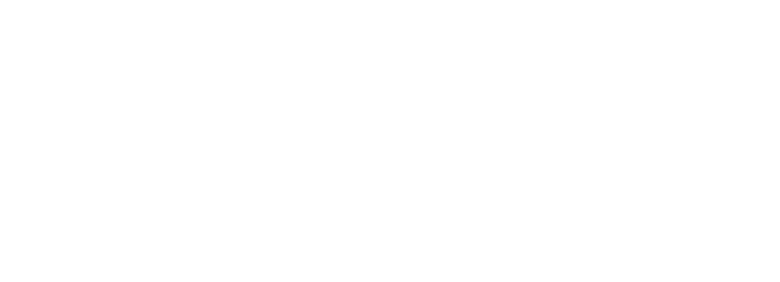
In recent years, economic growth has brought soaring labor costs in China, once the world's leading producer, and the traditional labor-intensive business model has begun to show signs of slowing down. Under such circumstances, there is an accelerating trend toward "manpower saving," the automation of processes that used to be handled by specialized machines or manual labor. In addition, the production system is changing from mass production of standardized products to high-mix low-volume production, and FA equipment manufacturers are required to respond to new "automation needs" to support the maintenance of quality and production volume.
Company I, a developer and manufacturer of various automatic machines and assembly machines, recently embarked on the development of a new, more versatile automatic assembly machine to meet the growing need for labor savings at production sites in China. Immediately after starting development, however, the company was confronted with a technical problem.
In order to assemble the new model not only from the top but also from the side or at an angle on a complex structure, we decided to incorporate a tilt mechanism to tilt the table, but we were unable to find the best system. The first prototype of the pneumatic control system, which was the cheapest and simplest method, did not provide the desired accuracy because the tilting motion of the table was too cumbersome.
The mechanism for tilting the table must be able to stop the table quickly at a predetermined angle with high accuracy. Since pneumatic control was insufficient to achieve this accuracy, Company I was considering a different mechanism. Mr. K, the manager in charge of the company's development department, said, "The air control system was not sufficient to achieve the required accuracy.
"Both servo systems and Stepping Systems have their advantages and disadvantages. Servo systems offer high accuracy, but the parameter settings are complicated and expensive. Stepping Systems have cost advantages, but we were concerned about loss of synchronization. When the load changes depending on what is assembled, we were not sure whether loss of synchronization could be prevented by simply taking a margin. Furthermore, increasing the capacity would result in the device becoming larger... Because this is a key mechanism for the device, we had to find a solution somehow. We were looking for a mechanism that would solve all of these issues at the same time."
Mr. K consulted with a sales representative from SANYO DENKI, with whom he had done business on other products, about these issues. The sales representative then suggested the closed-loop Stepping Systems" SANMOTION Model No.PB ( Closed Loop )" Mr. K was intrigued by the idea that "it is entirely possible to achieve the required performance by 'combining the best of' servo systems and Stepping Systems" and he immediately asked them to help him select a system.
When Mr. K saw the results of his selection later, he was surprised at how small the motor size was.
"The motor was smaller than I expected, so I was a bit worried, but when I checked, I found out that SANMOTION Model No.PB ( Closed Loop ) has high torque at low speeds and when stopped, so for this type of application it can be made smaller than a servo motor." (Mr. K)
Furthermore, what caught Mr. K's attention was the feature that Stepping Systems does not suffer from "step-out," a weakness of the system.
"Just like a servo, it uses closed-loop control that uses an encoder to control positioning, so it doesn't go out of step, and just like a stepper, it can move quickly over short distances and achieve precise positioning. In addition, because it has position correction control, there will be no positional deviation even if the load on the item being assembled changes, so you can expect high precision." (Mr. K)
Another major advantage was that it did not require complex parameter settings, as is the case with Stepping Systems.
In addition, the recommended driver was programmable and could be easily positioned by specifying points externally via I/O. Since we could easily control it with general-purpose I/O, we were able to start working on the prototype right away. It also reduces the burden on upper management and, above all, on the design team. (Mr. K)
As a result of the actual machine testing, it was confirmed that the operating characteristics, which combine the advantages of servo systems and Stepping Systems, improved the reliability of the equipment and shortened the cycle time. In addition to these features, the fact that the cost was significantly lower than that of a servo system also supported Mr. K's decision to introduce the system.
Thus, Company I, which had determined that it could expect maximum performance improvement at minimum cost, soon decided to adopt "SANMOTION Model No.PB ( Closed Loop )" Mr. K said:
"We have succeeded in developing a product that stands out from the crowd and is pleased to be able to contribute to increasing the efficiency and speed of our customer's production lines."
For more information about stepping motors, please see "What is a stepping motor? An explanation of its structure, types, usage (drive system and control method), advantages and features."
Published On: