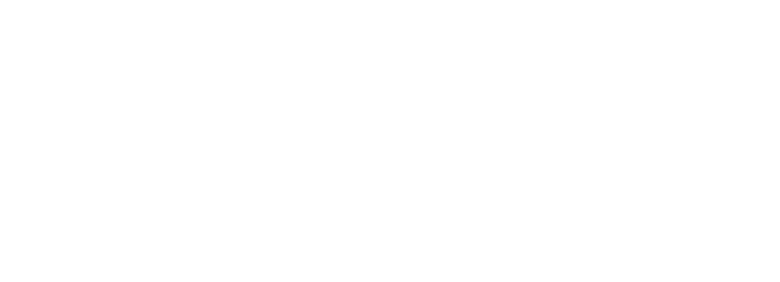
Company F was working on developing a new model of automated clinical chemistry analyzer. However, despite a process of trial and error aimed at improving the cycle time of testing, they faced one problem after another.
Mr. T from the Product Development Department had this to say:
"To improve the testing speed of the new model, we tried to shorten the cycle time by making the mechanism lighter and increasing the motor speed. However, we found that the reagent dropping mechanism would sometimes become misaligned. When we investigated the cause of the misalignment, we found that the stepping motor had lost synchronization."
Mr. T thought that the cause of the step-out was insufficient torque. Therefore, as a countermeasure to the step-out, he decided to increase the drive current of the driver to compensate for the lack of torque.
"Increasing the drive current solved the problem of step-out, but the motor generated more heat than expected, and the ambient temperature rose. Heat generation was likely to have a negative effect on the specimen, which was fatal for the testing device." (Mr. T)
Mr. T repeatedly made prototypes and tested them in order to keep the heat generation within an acceptable range. However, he was unable to obtain good results and time just passed by.
SANYO DENKI fan was used to cool the device's control unit. Therefore, Mr. T decided to consult with SANYO DENKI to get advice on heat countermeasures. After checking the requirements of the device in detail, the person in charge suggested replacing the motor.
"We received a suggestion that a closed-loop Stepping Systems Stepping Systems would be effective in reducing heat generation in the motor. Unlike Stepping Systems, closed-loop stepping systems incorporate a feedback loop like a servo system.
Therefore, the required torque is controlled according to the load, and only the necessary amount of current is passed, which minimizes heat generation. In addition, there is no need to worry about step-out, which can cause positional deviation, so the device is more resistant to load fluctuations caused by aging, and we can expect stability as a device." (Mr. T)
After receiving a more detailed explanation from a SANYO DENKI representative, Mr. T immediately began evaluating the prototype.
"Because we were originally using a pulse train input type driver, we were able to easily replace our current stepping driver with this one without having to change the drive profile for connecting to the host device. And we were successful in achieving our target of shortening the cycle time.
"Thanks to SANYO DENKI 's proposal, we were able to bring the new model to market as scheduled. In addition, the closed-loop Stepping Systems has the added benefit of reducing noise due to its low vibration," said Mr. T.
Up until now, Company F has mainly used stepping motors in its equipment.
"Through this development, we learned about the various benefits of the closed-loop Stepping Systems, so we would like to expand this to other equipment in the future," said Mr. T.
For more information about stepping motors, please see "What is a stepping motor? An explanation of its structure, types, usage (drive system and control method), advantages and features."
release date: