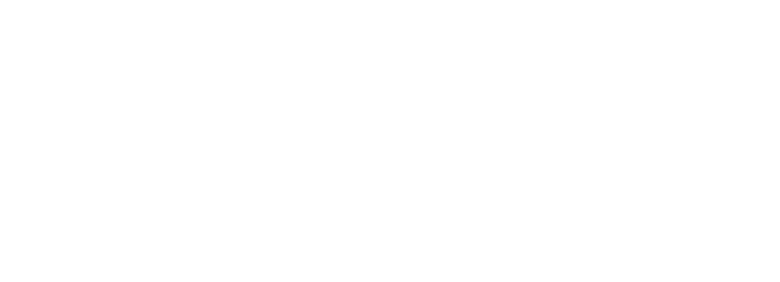
The market for sealing machines, automatic application devices that apply adhesives and sealants in automated manufacturing lines, is also expanding around the world. F Company, which manufactures and sells sealing machines, has now decided to develop a new model of sealing machine that is compatible with EtherCAT. Mr. H of the System Development Department at F Company says the following.
"Since EtherCAT has been adopted by major manufacturers, the devices in production lines are increasingly becoming EtherCAT compatible. We decided to look for an EtherCAT-compatible Motion Controller to improve compatibility with other production line devices."
Another challenge for the new equipment was to make it compact and space-saving.
"With current PLCs, you need to add a pulse train unit and driver each time you add another motor axis. Adding more units also increases the number of wires, which requires more space in the switchboard to house them. This equipment configuration was a bottleneck in our efforts to make the device more compact," said Mr. H.
Furthermore, the new equipment needed to be faster than the previous model in order to improve cycle time. The role of a sealing machine is to efficiently apply a set amount of adhesive to a set position. The objects to be applied are not only straight lines, but also a mixture of curves such as arcs. For this reason, it was necessary to draw an accurate trajectory by adjusting the positions and speeds of multiple motors.
Mr. H began searching for an EtherCAT-compatible Motion Controller that could achieve trajectory control, but he was unable to find Motion Controller that met his requirements and reached a dead end.
Searching for a solution, Mr. H consulted with a SANYO DENKI sales representative who was visiting F regularly for another reason. The sales representative listened to the details of the current issues and system requirements, and later proposed Motion Controller" SANMOTION C CS100."
"Motion Controller SANMOTION C S100 supports the cyclic position control mode of the EtherCAT specification, and can achieve highly accurate trajectory operation by commanding the position of each axis at a communication cycle of 2/1000 seconds. Other companies' EtherCAT controllers use a profile position control mode that specifies the coordinates and speed of the target position, so it is not possible to control the trajectory during positioning. With the SANMOTION C S100, we can expect to improve cycle times while maintaining the operating accuracy of the sealing machine. In addition, since it is equipped with a web server function that can monitor the operating status and read and write program variables using a general-purpose browser on a PC, we thought that it would be easy to deploy a system that supports IoT (*2)." (Mr. H)
Furthermore, we received a proposal to save space by using Motion Controller" SANMOTION C S100" and a multi-axis system. "There is a case where the control equipment space has been minimized by combining the industry's smallest Motion Controller" SANMOTION C S100" with the multi-axis closed-loop Stepping Systems" SANMOTION Model No.PB ( Closed Loop ) "
In previous equipment, three motors were controlled by three drivers, but by using SANYO DENKI 's multi-axis closed-loop Stepping Systems, "SANMOTION Model No.PB ( Closed Loop )," three motors can be controlled by one driver. With EtherCAT, devices can be connected with just one cable, which significantly reduces the space required for cable wiring. As a result, we expect to be able to minimize the space required for control equipment to one-third that of previous equipment." (Mr. H)
With the support of SANYO DENKI, Mr. H immediately incorporated Motion Controller" SANMOTION C CS100" into the prototype and began evaluation.
"While supporting EtherCAT, we were able to achieve significant space savings and shorten the cycle time while maintaining the accuracy of adhesive application. Furthermore, the reduced wiring labor has also significantly reduced maintenance labor. We have received high praise from our customers, and we are very grateful to SANYO DENKI." (Mr. H)
(*1) Model number: In case of SMC100. Compared to Motion Controller with built-in digital I/O that can handle sequence, motion and robot control in one unit. According to our research as of October 10, 2018.
(*2) Internet of things: A system in which all kinds of things are connected to a network and mutually controlled by exchanging information.
For more information about stepping motors, please see "What is a stepping motor? An explanation of its structure, types, usage (drive system and control method), advantages and features."
release date: