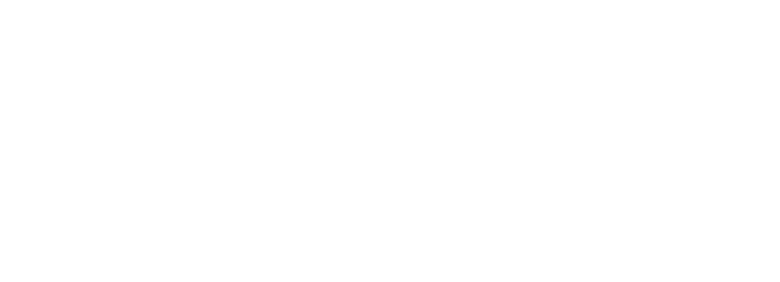
Company H, a food processing machine manufacturer, was approached by a food manufacturer asking if it was possible to speed up their processing machines. Mr. E of the R&D department at Company H said the following:
"Our food processing machines are customized as dedicated machines to suit the food products that our customers are processing. By adding optional mechanisms, we can process multiple food items, so up until now, we often operated multiple processing machines to adjust production volume. However, our customers asked us to increase the processing speed and reduce the labor required for changeovers so that we could flexibly respond to increases in production volume, such as during busy periods. We also considered making the equipment more compact so that it could be placed in tight spaces."
Meeting these demands posed several technical challenges. "The biggest problem was the motor. The current model was equipped with an induction motor. A reduction gear was used to compensate for the lack of torque, and the speed was controlled by Inverter.
Due to the nature of the material, if the line is stopped during breaks, the material will dry out and harden. A large torque is required to restart, so one of the conditions for selecting a motor was that it would operate reliably during this restart. However, induction motors have the characteristic that torque is at its maximum at the rated speed and is difficult to produce at low speeds, so to match the required torque at low speeds, we needed to select a motor with a large torque margin. " (Mr. E)
Mr. E was looking for a solution. At first, we built a prototype to increase the speed by changing the speed reducer without changing the current motor. However, when we reduced the reduction gear ratio, the motor sometimes failed to restart due to insufficient torque in the low-speed range, so we needed to increase the motor capacity. Not only did this increase the size of the motor, but it also resulted in increased heat generation. Since heat generation affects food quality, we decided not to go ahead with this proposal.
Next, we considered increasing the number of machining lines in the machine and operating them in parallel. However, we decided against this idea as well, because the mechanical mechanism would have become more complicated, leading to higher costs. It was difficult to find a solution. (Mr. E)
Company H had received similar issues from several customers, and an immediate response was required.
Mr. E, who was looking for a replacement motor, consulted SANYO DENKI was introduced to him by an engineer he knew.
To solve Mr. E's problem, SANYO DENKI representative proposed the closed-loop Stepping Systems" SANMOTION Model No.PB ( Closed Loop )" Mr. E was surprised by the content of the proposal.
All the motors I have used so far have been induction motors. We had never paid attention to the torque-speed characteristics of motors, so we did not know that there were motors that produce more torque at lower speeds. We had selected motors based on the condition that they operate reliably at startup, but the motor you proposed this time was 1/5th the size and 1/10th the weight of the motors in our current machines. We were surprised that a motor of such a small size could work without any problems. We also learned that the motor is controlled so that current flows only when torque is needed, which also reduces the heat generated by the motor. (Mr. E)
However, Mr. E still had concerns. I had an image that control motors are difficult to set up, so I was worried that operation would be complicated," he said. However, I found that the speed can be easily adjusted with a switch. This will be easy for our customers to use.
Furthermore, we found that it was possible to control four motors with one driver. Until now, one Inverter was needed for each motor, so we can also expect to be able to downsize the control unit. I thought this was truly the ideal proposal for solving this issue." (Mr. E)
Mr. E began developing a food processing machine incorporating a "closed-loop Stepping Systems." With support from SANYO DENKI, he successfully completed the new model. "The processing speed of the new model is twice as fast as the current machine. There is also no longer any protruding part in the motor, which has made it possible to miniaturize the device. Thanks to their help, we have completed a food processing machine that can flexibly respond to changes in production volume, type of ingredients, or condition, and our customer is very satisfied with it." (Mr. E)
For more information about stepping motors, please see "What is a stepping motor? An explanation of its structure, types, usage (drive system and control method), advantages and features."
release date: