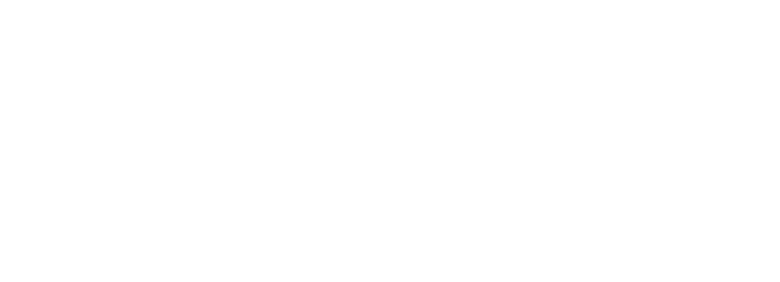
Company M, which manufactures and sells bread and confectionery machinery and kitchen machinery, was working on developing a new model of bread dough fermentation control system. Mr. U, who is in charge of development, said the following.
"Our goal was to create a device that could optimally manage fermentation for various types of bread. In the new model, we decided to install a fan to make the temperature and humidity inside the oven more uniform and prevent uneven fermentation.
We needed to control the airflow according to the function of each mode and keep the temperature and humidity inside the oven constant without drying out the dough, so we tried to control the airflow with voltage. However, the range in which the airflow could be changed was narrow, and the fan rotation became unstable.
Furthermore, since the humidity inside the warehouse is high and there is a lot of dust flying around, the dust-proof and waterproof performance of the fan was also an important requirement.
Mr. U began gathering information in order to find fans who met these conditions.
As Mr. U continued to gather information, he visited SANYO DENKI booth at an exhibition and discussed his issues. Later, a SANYO DENKI representative visited M Company and discussed the issues in detail.
"The SANYO DENKI representative suggested Splash Proof Fan with protection class IP68 for dust and water resistance. This fan also has PWM control function, so we were told that we could easily control the optimal airflow." (Mr. U)
Mr. U implemented the proposed Splash Proof Fan in a prototype and immediately began evaluating it.
"This was the first time we performed PWM control, but thanks to the box-type PWM Controller proposed for evaluation purposes, the evaluation was very easy and we were able to significantly reduce the evaluation time." (Mr. U)
As a result of the evaluation, the fan performed as expected, so Company M began considering adopting it.
"When we implemented the fan, the standard lead wires were not long enough, but extending them by splicing them would have created joints, which raised concerns about hygiene and environmental resistance. When we consulted SANYO DENKI about this problem, they proposed customizing the lead wires to be longer. This eliminated the need for connectors and the joints, reducing the design labor and costs of the protection measures. This additional proposal also helped to shorten the development period. We look forward to making more proposals like this from SANYO DENKI in the future." (Mr. U)
防水ファンについて詳しくは「防水ファンとは?」もご覧ください。
release date: